15 Hinterachse/Aufhängung/Gelenkwelle
Inhalt
Arbeitspositionen
ALLGEMEINES
Die Capri II - Fahrzeuge
sind analog der bisherigen Modellreihe mit Hinterachsen zwei verschiedener
Bauarten ausgestattet. Im nachfolgenden Allgemeintext und in der
Reparaturbeschreibung werden diese Hinterachsen mit "D" und
"J" - Hinterachse benannt.
Hinterachse
Bei der
"D"-Hinterachse ist das Ausgleichgetriebe direkt im Achsgehäuse
gelagert. Für eventuell auftretende Reparaturen im Hinterachsgetriebe
muss die Hinterachse ausgebaut werden.
Die
"J"-Hinterachse ist durch ein abschraubbares Hinterachsgetriebe
- d.h. einem Träger mit Ausgleichgetriebe - gekennzeichnet. Reparaturen
am Hinterachsgetriebe erfordern dementsprechend keinen Ausbau der
Hinterachse, sondern lediglich des Hinterachsgetriebes.
Aufhängung
Die Hinterachsaufhängung
erfolgt durch zwei parallel zur Fahrzeuglängsachse angeordnete
halbelliptische Längsblattfedern, einem Querstabilisator und zwei
Teleskopstoßdämpfern.
Gelenkwelle
Zur Übertragung der
Antriebskraft vom Getriebe auf die Hinterachse werden einteilige und
geteilte Gelenkwellen verwendet. Die geteilte Gelenkwelle ist mit einem
Mittellager und zusätzlichem Kreuzgelenk bzw. Gleichlaufschiebegelenk
versehen. Beim Einbau einer Gelenkwelle mit Gleichlaufschiebegelenk ist unbedingt
auf die Einbaufolge in Position 15 514 zu
achten.
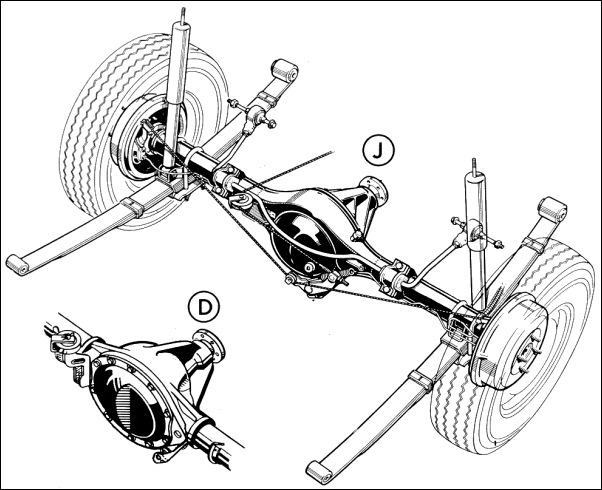 |
Abb. 1
Hinterachsen "D" und "J" |
FUNKTIONSBESCHREIBUNG
Hinterachse
Das Antriebskegelrad läuft auf
zwei Kegelrollenlagern, die in der "D"-Hinterachse durch
einen Distanzring und in der "J"-Hinterachse durch eine
Schrumpfhülse (Zusammendrücken der Hülse durch Anziehen der
selbstsichernden Mutter - Antriebskegelrad) vorgespannt werden,
Abb.2 und Abb.3. Die richtige Eingriffstiefe des Kegelrades in das
Tellerrad wird durch passende Distanzscheiben, die zwischen
Kegelradkopf und hinterem Kegelrollenlager eingesetzt sind,
erzielt.
Das Tellerrad ist mit dem Ausgleichgetriebe verschraubt und läuft
mit diesem ebenfalls auf zwei Kegelrollenlagern. Bei der
"D"-Hinterachse werden beide Lager durch Rückfederung
des Achsgehäuses nach dem Spreizen vorgespannt (Ausgleichscheiben
zwischen Ausgleichgetriebegehäuse und Kegelrollenlager, Abb.2).
Das Vorspannen der Kegelrollenlager vom Ausgleichgetriebe der
"J"-Hinterachse erfolgt durch Verstellen der seitlichen
Ringmuttern, Abb.3. Der Kraftfluss erfolgt bei beiden Hinterachsen
über je zwei Ausgleich- und Seitenwellenkegelräder zu den beiden
Hinterachsseitenwellen.
Die Hinterachswellen sind durch eine Vielkeilverzahnung mit dem
Hinterachswellenkegelrädern im Ausgleichgetriebe verbunden und
laufen an ihren äußeren Enden in Kugellagern. Die Kugellager
sind mit einem Dichtring versehen, der das Achsgehäuse nach innen
hin abdichtet.
|
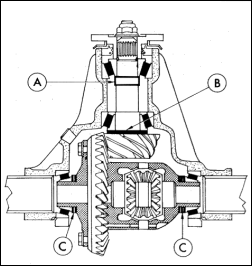
Abb. 2
"D"-Hinterachse
A = Distanzring
B = Ausgleichscheibe Antriebs-
Kegelrad
C = Scheiben Ausgleich-
Getriebegehäuse
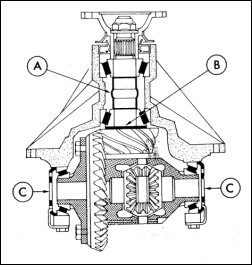
Abb. 3
"J"-Hinterachse
A = Schrumpfhülse
B = Ausgleichscheibe Antriebskegelrad
C = Ringmuttern
|
Aufhängung
Die halbelliptischen
Längsblattfedern sind in ihren Aufhängungen an den
Längsträgern der Bodengruppe in Silentbüchsen bzw.
Gummibüchsen gelagert, um die Übertragung von Rollgeräuschen
und Vibrationen auf die Karosserie zu verhindern. Die Hinterachse
ist an den Federn asymmetrisch befestigt, d.h. der Abstand zu der
vorderen Federaufhängung ist kürzer als zu der hinteren. Dadurch
wird das Aufschaukeln der Federn während der Beschleunigung oder
bei Befahren von schlechten Straßen verhindert.
Hydraulische, doppelwirkende Teleskop-Stoßdämpfer sind zwischen
Hinterachse und Bodengruppe angeordnet. Durch eine hermetische
Abdichtung erfordern sie keinerlei Wartung.
Zusätzlich gelangt ein als Drehstabfeder ausgelegter Stabilisator
zum Einbau. Damit wird eine Minderung der Rollneigung und ein
besseres Eigenlenkverhalten des Fahrzeuges erreicht. In
Lagergummis eingefasst, ist der Stabilisator durch zwei
Haltebügel drehbar an den Hinterachsrohren befestigt. Die beiden
aufgeschraubten Endstücke sind mit Silentbüchsen versehen und an
den Längsträgern der Bodengruppe angeschraubt. Beim Aus- und
Einbau des Stabilisators sowie beim Auswechseln der Silentbüchsen
sind die Reparaturhinweise in den Positionen 15 752 und 15 756 4
zu beachten.
Gelenkwelle
Die Gelenkwellen sind einerseits über ein Kreuzgelenk mit der
Getriebeabtriebswelle (Vielkeilverzahnung) und auf der anderen
Seite über ein Kreuzgelenk mit dem Flansch des Antriebskegelrades
verbunden. Die geteilten Gelenkwellen sind unmittelbar hinter dem
Zwischenlager mit einem dritten Kreuzgelenk bzw.
Gleichlaufschiebegelenk versehen, Abb.5 und Abb.6.
|
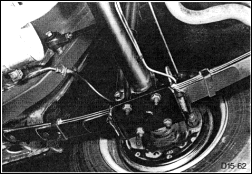
Abb. 4
Hinterachsaufhängung
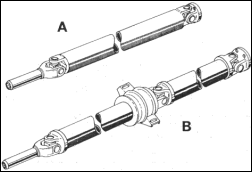
Abb. 5 A =
einteilige Gelenkwelle
B = geteilte Gelenkwelle mit
Kreuzgelenk
|
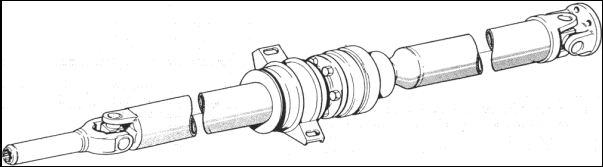
Abb. 6 Geteilte
Gelenkwelle mit Gleichlaufschiebegelenk. Beim Einbau dieser Welle ist auf die
Einbaufolge in Position 15 514 zu achten.
|
Einbautabelle -
Hinterachse und Gelenkwelle
Capri
II |
Motor |
Hinterachse |
Gelenkwelle |
"D" |
"J" |
einteilig |
geteilt |
FoG |
1,3 HC |
|
x |
|
x |
1,6 HC |
x |
x |
|
x |
1,6 HC (GT) |
x |
x |
|
x |
2,3 HC |
x |
|
|
x |
3,0 HC |
x |
|
|
x |
FoB |
1,3 HC |
|
x |
x |
|
1,6 HC |
|
x |
|
x |
1,6 HC (GT) |
x |
x |
|
x |
2,0 HC |
x |
|
|
x |
3,0 HC |
x |
|
|
x |
FoG: Ford Deutschland
FoB: Ford England
PRÜFUNG UND EINSTELLUNG
Zum Überprüfen des Ölstandes muss
das Fahrzeug auf ebenem Boden stehen. Den Füll- bzw.
Ölstandstopfen entfernen. Der Ölspiegel soll bis zur Unterkante
der Einfüllöffnung reichen. Falls erforderlich, vorgeschriebenes
Öl auffüllen. Stopfen wieder einsetzen.
|
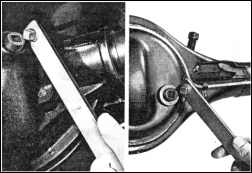
Abb.
7 Ölstandstopfen an den Hinterachsen
|
SPEZIALWERKZEUGE
Englische
Ausführung |
Europäische
Ausführung |
Deutsche
Ausführung |
|
Werkzeug-Bezeichnung |
15-008
|
Messblock |
15-008-03
|
Stufenblock |
15-019
(P-4133) |
 |
15-019
(G2-4209-B) |
|
Messwelle |
15-020
(P-4134) |
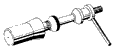 |
15-020
(G2-4209-C) |
|
Meisterritzel
|
15-021
(P-4136) |
 |
15-021
(G3-4209-A) |
|
Differentiallager-Einstellung, Druckspindel |
15-022
(P-4008) |
 |
15-022
(G2-4209-E) |
|
Messuhrhalter |
15-023
(P-4135) |
 |
15-023
(G2-4209-F) |
|
Druckmessgerät |
15-024
(P-4137) |
 |
15-024
(G3-4209-B) |
|
Messbüchse |
15-025
(P-4128) |
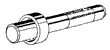 |
15-025
(G3-4221-B) |
|
Differentiallager, Aufpressdorn |
15-026 |
 |
15-026
(G3-4221-A) |
|
Differentiallager, Abzieher |
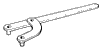
15-030
|
Universal Flanschhalteschlüssel |

15-031
P-4080 |

15-031
(G2-4221-B) |
|
Differentiallager, Aufpressdorn |

15-033
(P-4127-A) |

15-033
(G3-4116-B) |
|
Lagerlaufringe-Achsgehäuse, Einzieher |

15-034
(P-4013-3) |

15-034
(G2-4616-B) |
|
Lagerlaufringe-Achsgehäuse, Einzieher |
15-041
(P-4131) |
 |
15-041
(547-D) |
|
Drehmomentlehre |
15-042
(G2-4621-B) |
 |
15-042
(G2-4621-B) |
|
Antriebskegelradlager, Aufpressdorn |
15-043
(P-4015-A) |
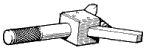 |
15-043
(P-4015-A) |
|
Lagerlaufringe-Achsgehäuse, Aufpressdorn |
15-046
(SM-991-A) |
 |
15-046
(4201) |
|
Messuhr mit mm Einteilung |
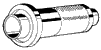
15-047-A
|
Dichtring-Antriebskegelrad, Einbaudorn |

15-048
P-4130-A |

15-048
(G2-4676-A1) |
|
Dichtring-Antriebskegelrad, Auszieher |

16-009
P-4077-A |

16-009
(G2-4200) |
|
Aufspannvorrichtung, Hinterachse |
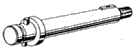
21-023
|
Universalwelle |
G1-1225
|
Seitenwellenlager Auf- und Abzieher
(Hauptwerkzeug) |
G2-1225-A1
|
Seitenwellenlager Abzieher
(Zusatzstück für G1-1225) |
G2-1225-B1
|
Seitenwellenlager Aufzieher
(Zusatzstück für G1-1225 |
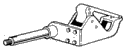
P-4138 |

G3-4200 |
|
Aufspannvorrichtung, Hinterachse |
G3-4621-A
|
Antriebskegelradlager, Abzieher |

P-4000-28 |

G2-4621-A1 |
|
Antriebskegelradlager-Abzieher |

P-4129-B |

G2-4676-A |
|
Dichtring-Antriebskegelrad, Einpressdorn |

6312-A |

G2-4851-A |
|
Flanschabzieher |
370
|
Grundplatte |
550
|
Handgriff |
P-4009
|
Differentiallager-Vorspannung, Messvorrichtung |
P-4084
|
Seitenwellenlager, Presssitzlehre |
P-4090-2
|
Seitenwellenlager, Aufzieher
(Zusatzstück für 370) |
P-4090-6
|
Seitenwellenlager Abzieher
(Zusatzstück für 370 |
P-4090-12-A
|
Antriebskegelradlager, Abzieher
(Zusatzstück für 370) |
15-008-03
15-001 |
 |
15-008-03
15-001 |
|
Einstellblöckchen für Stufenlehre
G2-4209-A |
15-008-03
P-4132-B |
 |
15-008-03
G2-4209-A |
|
Stufenlehre |
15-019 
P-4075
|
Messwelle |
15-020 
P-4075-4
|
Meisterritzel |
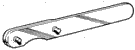
15-030
P-4097 |
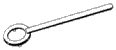
15-030
G2-4851-B |
|
Flanschhalter |
15-030 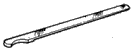
C-4114
|
Flanschhalter |
CP-4013-A
|
Lagerlaufringe-Achsgehäuse, Einzieher
(Hauptwerkzeug) |
Achtung
Folgende Darstellungen wurden für die Werkzeugabbildungen und -nummern
gewählt:
-
Bei den in der Mitte
der Bildleiste gezeigten Werkzeugen handelt es sich um
Europa-Werkzeuge. D.h. das Werkzeug wird vom deutschen und
englischen Lieferanten gefertigt und mit der gleichen Nummer
benannt.
Beispiel: 15-6/15-008
-
Befindet sich unter
der Europa-Nummer eine weitere Nummer in Klammern gesetzt, so
handelt es sich dabei um die alte Werkzeugnummer. Dieses Werkzeug
ist in Deutschland und England gleich und wurde jetzt nur mit einer
Europa-Nummer versehen.
Beispiel: 15-7/15-041
-
Werkzeugnummer weiß
im schwarzen Feld: Dieses Werkzeug wird nicht mehr hergestellt und
durch das gegenüberstehende Werkzeug ersetzt.
Beispiel: 15-7/15-033 deutsches Werkzeug entfällt
15-7/15-034 englisches Werkzeug entfällt
ARBEITSPOSITIONEN
|
15 212
HINTERACHSE MIT AUFHÄNGUNG AUS- UND EINBAUEN |
|
KEIN
SPEZIALWERKZEUG ERFORDERLICH
|
|
Ausbauen
- Fahrzeug unter den
Längsträgern aufbocken, Wagenheber unter der Hinterachse
lassen.
- Gelenkwelle vom Flansch
Antriebskegelrad abbauen.
- Handbremsseil am Zwischenhebel
der Hinterachse lösen und herausziehen, Abb.8.
- Bremsschlauch von
Bremsrohrleitung hinten rechts trennen und Leitung gegen
auslaufende Bremsflüssigkeit verschließen, Abb.9.
- Beide Stoßdämpfer vom
Hinterachsgehäuse abbauen. Hierzu den Achskörper mit einem
Wagenheber anheben.
- Stabilisator vom Längsträger
Bodengruppe abbauen, Abb.10.
- Federgehänge hinten (je zwei
Laschen) und Bolzen (2) der vorderen Federaufhängung
ausbauen. Federenden, falls erforderlich, mit einem
Schraubendreher aus den Federböcken drücken, Abb.11.
- Hinterachse komplett mit
Aufhängung absenken und herausheben.
|
Abb. 8
Zwischenhebel - Handbremse
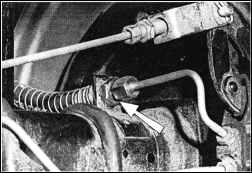
Abb. 9
Bremsschlauch an Bremsrohrleitung
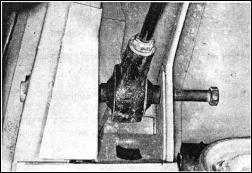
Abb.10
Befestigung - Stabilisator an
Bodengruppe
|
Einbauen
- Hinterachse komplett mit
Aufhängung mittels Wagenheber in Einbaulage heben. Vordere
Federenden in die Federböcke einsetzen und Federbolzen von
innen nach außen einführen. Muttern noch nicht festziehen.
- Federgehänge einbauen, falls
erforderlich, Gummibüchsen im Längsträger auswechseln.
Muttern noch nicht festziehen, Abb.11.
- Stabilisator an Längsträger
Bodengruppe anbauen, Muttern noch nicht festziehen.
Stoßdämpfer an Hinterachsgehäuse montieren, Abb.12.
- Handbremsseil an Zwischenhebel
der Hinterachse befestigen und so einstellen, dass der Hebel
vom Anschlag etwas abhebt, Abb.8.
- Gelenkwelle an Flansch
Antriebskegelrad anbauen (neue Federringe verwenden).
Schrauben mit vorgeschriebenem Drehmoment festziehen, Abb.13.
- Bremsschlauch an
Bremsrohrleitung anschließen und hinteren Bremskreis
entlüften, Fahrzeug ablassen.
- Muttern der vorderen und
hinteren Federaufhängung sowie Muttern Stabilisator an
Bodengruppe mit vorgeschriebenem Drehmoment festziehen.
Alle Muttern, Hinterfeder bzw. Stabilisatorbefestigung an
Bodengruppe, dürfen nur unter Belastung der Feder, d.h. im
eingefederten Zustand, festgezogen werden.
|
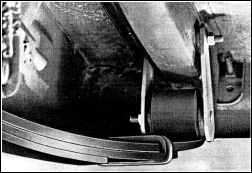
Abb.11
Federgehänge hinten
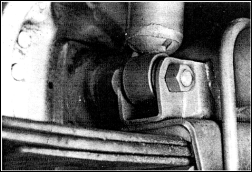
Abb.12 Untere
Stoßdämpferbefestigung
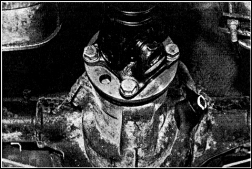
Abb.13
Gelenkwelle an Flansch
Antriebskegelrad
|
|
15 214
HINTERACHSE AUS- UND EINBAUEN |
|
KEIN
SPEZIALWERKZEUG ERFORDERLICH
|
|
Ausbauen
- Radmuttern lösen, Fahrzeug
unter den Längsträgern aufbocken und Hinterräder abbauen.
- Gelenkwelle vom Flansch
Antriebskegelrad abbauen, Abb.14.
- Handbremsseil am Zwischenhebel
der Hinterachse lösen und herausziehen.
- Bremsrohrleitung vom
Bremsschlauch hinten rechts trennen und Leitung gegen
auslaufende Bremsflüssigkeit verschließen, Abb.15.
- Beide Stoßdämpfer von der
Hinterachse abbauen, hierzu den Achskörper mit einem
Wagenheber anheben.
- Beide Haltebügel des
Stabilisators von der Hinterachse abschrauben. Hierzu den
Stabilisator mit einem geeigneten Werkzeug nach hinten ziehen,
um die Schrauben spannungsfrei herausdrehen zu können,
Abb.16.
- Muttern der Federbügel
abschrauben. Federbügel entfernen und Hinterachse
herausheben.
|
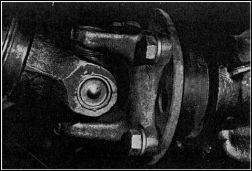
Abb.14
Gelenkwelle an Flansch
Antriebskegelrad
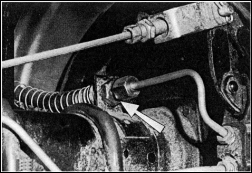
Abb.15
Bremsschlauch an Bremsrohrleitung
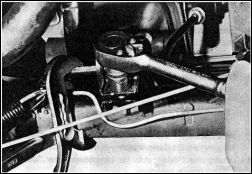
Abb.16
Befestigung Stabilisator an Hinterachse
|
Einbauen
- Hinterachse einsetzen, dabei
richtige Lage der Feder-Herzbolzen sowie der oberen Gummilager
beachten, Abb.17. Gelenkwelle lose an Flansch Antriebskegelrad
montieren (neue Federringe verwenden).
- Untere Gummilager,
Gegenplatten und Federbügel ansetzen (Korrekte Lager
beachten). Neue selbstsichernde Muttern verwenden und
mit vorgeschriebenem Drehmoment festziehen, Abb.17.
- Haltebügel auf Lagergummis
Stabilisator setzen. Stabilisator mit geeignetem Werkzeug auf
die Lagerböcke drücken, damit die Schraubenlöcher
zueinander ausgerichtet sind und die Schrauben spannungsfrei
eingedreht werden können. Schrauben mit vorgeschriebenem
Drehmoment festziehen.
- Stoßdämpfer an Hinterachse
montieren, Ab.18. Bremsrohrleitung an Bremsschlauch
anschließen. Hinteren Bremskreis entlüften.
- Handbremsseil am Zwischenhebel
der Hinterachse befestigen und so einstellen, dass der Hebel
vom Anschlag etwas abhebt, Abb.19.
- Schrauben Gelenkwelle an
Flansch Antriebskegelrad mit vorgeschriebenem Drehmoment
festziehen.
- Hinterräder montieren,
Fahrzeug ablassen und vorgeschriebenes Hinterachsöl
einfüllen.
|
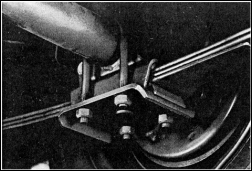
Abb.17
Befestigung Hinterachse an Federn
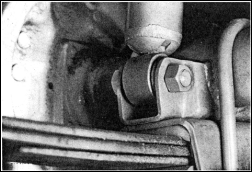
Abb.18 Untere
Stoßdämpferbefestigung
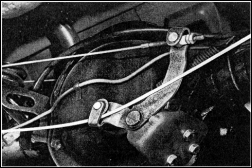
Abb.19
Zwischenhebel Handbremse
|
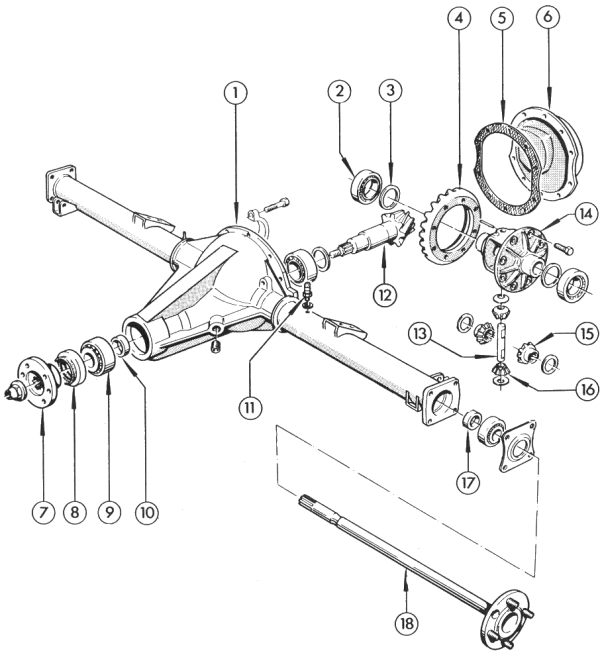 |
Abb.20
1 = Hinterachsgehäuse
2 = Kegelrollenlager Ausgleichgetriebe
3 = Ausgleichscheibe Ausgleichgetriebe
4 = Tellerrad
5 = Dichtung
6 = Deckel
7 = Flansch Antriebskegelrad
8 = Radialdichtring
9 = Kegelrollenlager Antriebskegelrad
10 = Distanzring Antriebskegelrad
11 = Entlüftungsventil
12 = Antriebskegelrad
13 = Welle Ausgleichkegelräder
14 = Gehäuse Ausgleichgetriebe
15 = Kegelrad Hinterachswelle
16 = Ausgleichkegelrad
17 = Haltering
18 = Hinterachsseitenwelle
|
|
|
15 214 8
HINTERACHSE ZERLEGEN UND ZUSAMMENBAUEN |
|
ERFORDERLICHES
SPEZIALWERKZEUG
Messblock
...............................................
Stufenblock .............................................
Messwelle ...............................................
Meisterritzel ............................................
Druckspindel ...........................................
Messuhrhalter .........................................
Druckmessgerät ......................................
Messring .................................................
Aufpressdorn Differentiallager ..................
Abzieher Differenziallager ........................
Flanschhalter ...........................................
Einzieher Lagerlaufringe ...........................
Drehmomentlehre .................................... |
15-008
15-008-03
15-019
15-020
15-021
15-022
15-023
15-024
15-025
15-026
15-030
15-033
15-041 |
|
|
Hinterachse zerlegen
- Bremsrohrleitung abmontieren.
Aufspannvorrichtung G3-4200/P-4138 am Hinterachsrohr
befestigen und Hinterachse in den Montageständer spannen.
Deckel mit Dichtung vom Hinterachsgehäuse entfernen (10
Schrauben) und Öl ablassen. Bremstrommeln, Seitenwellen mit
Bremsträger (je Seite 4 Schrauben) demontieren, Abb.21.
- Beide Lagerdeckel
Ausgleichgetriebe abbauen (4 Schrauben) und Ausgleichgetriebe
mit zwei angespitzten Vierkanthölzern aus dem Achsgehäuse
heben, Abb.22.
|
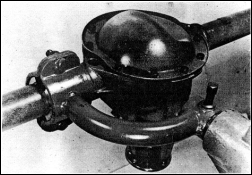
Abb.21
Hinterachse in Aufspannvorrichtung
G3-4200
an Montageständer
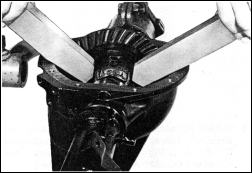
Abb.22 Gehäuse
Ausgleichgetriebe herausheben
|
- Flansch Antriebskegelrad mit
dem Spezialwerkzeug 15-030 festhalten und Mutter abschrauben,
Abb.23.
Da die selbstsichernde Mutter erneuert werden muss, ist die
jetzt abgeschraubte für Arbeitsgänge beim Zusammenbau
aufzubewahren.
- Flansch Antriebskegelrad mit
dem Spezialabzieher G2-4851-A/6312-A abziehen.
Antriebskegelrad aus dem Achsgehäuse nehmen, Abb.24.
- Großes Kegelrollenlager vom
Antriebskegelrad abziehen. Hierzu Abziehplatte mit Zugbolzen
G3-4621-A in Verbindung mit der Brücke des Abziehers
G2-4621-A1 oder Grundplatte 370 mit den Einsätzen P-4090-12-A
verwenden, Abb.25.
|
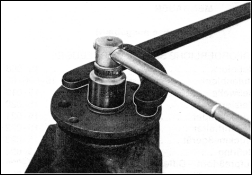
Abb.23 Flansch
Antriebskegelrad festhalten
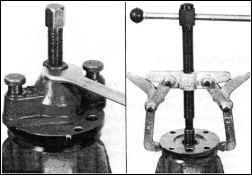
Abb.24 Flansch
Antriebskegelrad abziehen
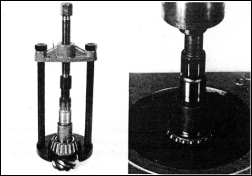
Abb.25
Kegelrollenlager abziehen
|
- Kleines Kegelrollenlager und
Radialdichtring mit dem Spezialdorn 15-042 gleichzeitig aus
dem Achsgehäuse entfernen, Abb.26.
- Kleinen Lageraußenring mit
dem Spezialdorn 15-043 heraustreiben und neuen Lageraußenring
mit dem Spezialwerkzeug 15-033 einziehen. Großen
Lageraußenring auf gleiche Weise erneuern (Die Druckstücke
des Einziehwerkzeuges haben jeweils auf einer Seite eine Stufe
zum Einziehen der Laufringe in die Hinterachse der früheren
Fahrzeugtypen, die im Ø kleiner waren), Abb.27.
Lageraußenringe unbedingt nacheinander auswechseln, damit
jeweils ein Lageraußenring als Führung des Einziehwerkzeuges
dient.
Lagersitze und Anlageflächen müssen frei von Beschädigungen
sein.
|
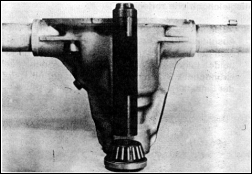
Abb.26 Kleines
Kegelrollenlager und
Radialdichtring
herausdrücken
Abb.27 A =
Lageraußenring heraustreiben
B = Lageraußenring einziehen
|
Ausgleichgetriebe zerlegen
- Abzieher 15-026 an ein
Kegelrollenlager des Ausgleichgetriebe-Gehäuses setzen und
mit einem Schenkel in den Schraubstock spannen. So beide Lager
abziehen. Bei Anwendung der Grundplatte 370 kann dieser
Vorgang mit Hilfe der Einsätze 15-006 ausgeführt werden,
Abb.28.
- Tellerradschrauben
herausdrehen und Tellerrad vom Gehäuse Ausgleichgetriebe
entfernen (8 Schrauben), Abb.29.
Spiel der Achswellenkegelräder einzeln mit einer
Fühlerlehre messen. Liegt das Spiel über dem
vorgeschriebenen max. Wert von 0,15 mm, muss es durch die
Montage von neuen Beilagscheiben (verschiedene Dicken siehe
Ersatzteilkatalog) verringert werden. Liegt das Spiel
darunter, ist ein Zerlegen des Ausgleichgetriebes bei
ordnungsmäßigem Zustand der Ausgleich- und
Achswellenkegelräder nicht erforderlich. Somit entfallen die
Punkte 10 bis 13, Abb.13.
|
Abb.28
Kegelrollenlager vom Ausgleich-
Getriebegehäuse abziehen
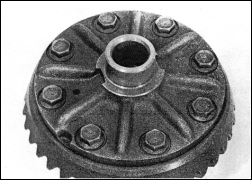
Abb.29
Befestigung Tellerrad Ausgleich-
Getriebegehäuse
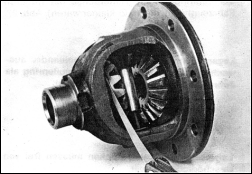
Abb.30 Spiel
der Achswellenkegelräder
messen
|
- Spannstift, der die Welle
Ausgleichgetriebe im Gehäuse sichert, mit passendem Dorn
heraustreiben, Abb.31, Welle Ausgleichgetriebe, Ausgleich- und
Achswellenkegelräder ausbauen.
Ausgleichgetriebe
zusammenbauen
- Achswellenkegelräder mit je
einer neuen Beilagscheibe in das Ausgleichgetriebegehäuse
einführen.
Gerillte Seite der Beilagscheiben muss zum
Achswellenkegelrad zeigen, Abb.32.
- Beide Ausgleichkegelräder mit
je einer Druckscheibe gleichzeitig zwischen die
Achswellenkegelräder drehen. Welle einschieben (Bohrung für
Spannstift beachten).
Spiel der Achswellenkegelräder einzeln mit einer Fühlerlehre
prüfen und sicherstellen, dass es nicht über dem max. Wert
von 0,15 mm liegt. Falls erforderlich, Ausgleichgetriebe
wieder zerlegen und stärkere Beilagscheiben einbauen.
- Welle Ausgleichgetriebe mit
einem Spannstift sichern, Abb.31.
- Tellerrad ca. 10 Minuten in
kochendem Wasser erwärmen, zu den Löchern des
Ausgleichgetriebe-Gehäuses ausrichten, neue
Originalschrauben eindrehen und mit vorgeschriebenem
Drehmoment festziehen (Kegelrollenlager noch nicht
aufpressen).
|
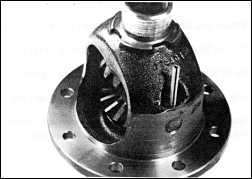
Abb.31
Spannstift Ausgleichgetriebewelle
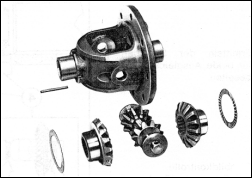
Abb.32
Ausgleichgetriebe zerlegt
|
Allgemeines über die Einstellung
von Teller- und Antriebskegelrad
- Teller- und Antriebskegelrad
bilden grundsätzlich eine Einheit und dürfen einzeln nicht
verwendet werden.
- Das im Text genannte
Spezialwerkzeug ist für die einzelnen Vorgänge
unerlässlich.
- Es ist auf unbedingte
Sauberkeit und Messgenauigkeit zu achten.
- Alle Lager- und Gleitstellen
sind beim Einbau mit dem vorgeschriebenen Hypoidöl
einzuölen.
- Die Innenteile einer komplett
eingestellten Achse können nicht ohne Einstell- und
Messvorgänge in ein anderes, gleiches Achsgehäuse eingebaut
werden.
Die Reihenfolge der Einstell-
und Messvorgänge ist unbedingt einzuhalten:
|
- Ermitteln der
Ausgleichscheibendicke für Antriebskegelrad.
- Messung des Gesamtspieles
(Ausgleichgehäuse mit Lager im Achsgehäuse).
- Ermitteln des
Distanzringes (Antriebskegelrad - Lagervorspannung).
- Ermitteln der Scheiben
für beide Ausgleichgetriebeseiten.
- Tragbildkontrolle.
a = Druckseite (Zug)
b = Schubseite
|
Abb.33
|
|
Ermitteln der
Ausgleichscheibendicke für Antriebskegelrad
- Ausgebaute Ausgleichscheibe
(oder eine neue Ausgleichscheibe beliebiger Dicke) und großes
Kegelrollenlager auf das Meisterritzel 15-020 schieben, Abb.34.
Für die Einstellung die Kegelrollenlager mit Hinterachsöl
benetzen.
- Meisterritzel in das Gehäuse
einsetzen und konische Mutter aufschrauben (Linksgewinde),
Abb.34; äußeres Lager und Griffstück aufschieben.
Druckmessgerät 15-023 aufschrauben. Griffstück der
Meisterritzels festhalten und Sechskant des Druckmessgerätes
bei neuen Lagern so lange im Uhrzeigersinn drehen, bis die
äußere Glocke des Werkzeuges auf die zweite
Strichmarkierung zeigt (bei gelaufenen Lagern auf die erste!).
Meisterritzel mehrmals drehen, damit sich die Lager
setzen können, Ab.35.
- Drehmomentlehre 15-041 aufsetzen
und das zum Drehen des Meisterritzels erforderliche Drehmoment
ablesen und notieren, Abb.36.
Dieses abgelesene Drehmoment ist unbedingt beim Einbau des
Antriebskegelrades einzuhalten. Werden z.B. 2,3 Nm (23 kpcm)
abgelesen, so muss dieser Wert auch nach der Montage des
Antriebskegelrades (+0,2 ... 0,4 Nm / 2 ... 4 kpcm) für den
Reibwert des Radialdichtringes wieder abgelesen werden.
|
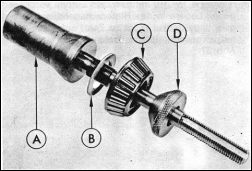
Abb.34
Meisterritzel 15-020
A = Meisterritzel
B = Ausgleichscheibe
C = Kegelrollenlager
D = Konusmutter
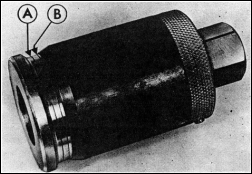
Abb.35
Druckmessgerät 15-023
A = Markierung für neue Lager
B = Markierung für gelaufene Lager
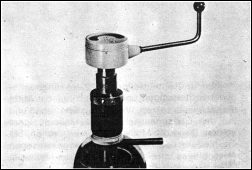
Abb.36
Durchdrehmoment des Meisterritzels
prüfen
|
- Messwelle 15-019 mit den zum
Einbau vorgesehenen Lagern in das Hinterachsgehäuse einlegen,
Lagerdeckel (Zahl zu Zahl) aufsetzen und mit vorgeschriebenem
Drehmoment festziehen, Abb.37.
- Messwelle mit einem geeigneten
Dorn festhalten und Stellmutter so lange nach außen drehen, bis
sich die Messwelle (nach Entfernen des Dornes) an der
Stellmutter noch von Hand drehen lässt, Abb.38. Messwelle
mehrmals drehen, damit sich die Lager setzen.
- Messuhr 15-046 im Halter 15-022
am Hinterachsgehäuse befestigen und Taststift auf die Mitte der
Messwelle setzen. Welle langsam drehen und auf den
Gesamtausschlag des Messuhrzeigers achten. Dann die Messwelle so
weit drehen, bis die Messuhr den halben Wert des gemessenen
Ausschlages anzeigt. Danach darf die Messwelle nicht mehr
gedreht werden, Abb.39.
|
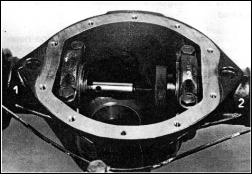
Abb.37 Messwelle
im Hinterachsgehäuse
eingelegt
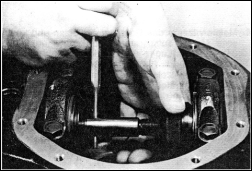
Abb.38 Messwelle
einrichten
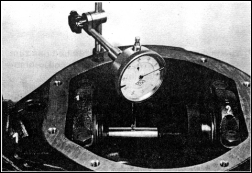
Abb.39 Messwelle
justieren
|
- Jetzt Taststift der Messuhr am
äußersten Rand der Meisterritzel-Stirnfläche in unmittelbarer
Nähe der Messwelle einrichten. Meisterritzel langsam drehen und
auf den Gesamtausschlag des Messuhrzeigers achten. Danach
Meisterritzel so weit drehen, bis die Messuhr den halben Wert
des gemessenen Ausschlages anzeigt. Nach diesem Vorgang darf das
Meisterritzel nicht mehr gedreht werden, Abb.40.
- Messuhr aus dem Halter entfernen
und in Messblock 15-008 montieren. Messblock mit Messuhr auf
eine geschliffene Fläche setzen und mit Hilfe des Stufenblocks
15-008-03 auf "0" stellen, Abb.41.
Auf dem Stufenblock sind jeweils unter den einzelnen Stufen
die Buchstaben der Hinterachscode eingraviert (Abb.41). Vor der
Messung der "D"-Hinterachse muss die Messuhr auf
dieser Stufe des Messblocks auf "0" gestellt werden.
- Messblock mit Messuhr auf die
Stirnflächenmitte des Meisterritzels setzen und mit dem
Taststift der Messuhr langsam quer über die Messwelle schieben.
Messuhr beobachten und genau die Stellung festhalten, in der der
Zeiger die Anzeigerichtung wechselt. Diesen Messvorgang öfter
wiederholen und genauestens durchführen.
Steht jetzt der Zeiger der Messuhr z.B. auf 95, so ist die
unter dem Meisterritzel liegende Ausgleichscheibe um 0,05 mm zu
Dick, Abb.42, wechselt der Zeiger die Anzeigerichtung bei 4, so
ist die Ausgleichscheibe um 0,04 mm zu dünn, Abb.43 (Hierbei
ist eine Messuhr mit Rechtslauf bei Einfedern des Taststiftes
vorausgesetzt!)
|
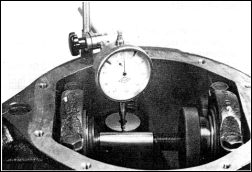
Abb.40
Meisterritzel justieren
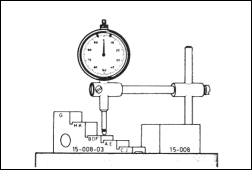
Abb.41 Messuhr
auf "0" stellen
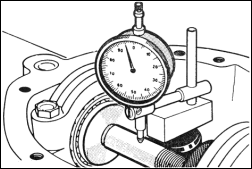
Abb.42
Messuhranzeige: 95 - Ausgleichscheibe
unter
dem Meisterritzel zu dick
|
Rechenbeispiel
Dicke der unter dem Meisterritzel
liegenden
Ausgleichscheibe:
1,01 mm
Messuhranzeige links von der
"0", z.B.
95:
- 0,05 mm
0,96 mm
Dieser Wert entspricht der Ausgleichscheibendicke, die zwischen
großem Kegelrollenlager und Antriebskegelradkopf beigelegt werden
muss.
- Mit der Mikrometerschraube eine
Ausgleichscheibe ausmessen, die dem ermittelten Wert entspricht
(Teil-Nummern der Ausgleichscheiben siehe Ersatzteilkatalog).
Kontrolle
- Meisterritzel ausbauen, alte
Ausgleichscheibe entfernen. Neue ausgemessene Scheibe und
Kegelrollenlager auf das Meisterritzel schieben und
Meisterritzel wieder einbauen. Konische Mutter aufschrauben,
Abb.44.
- Druckmessgerät aufschrauben
(bei neuen Lagern so weit festdrehen, bis die zweite und
bei gelaufenen Lagern die erste Markierung erreicht ist).
Meisterritzel mehrmals drehen, Abb.45.
|
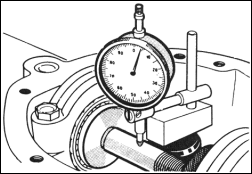
Abb.43
Messuhranzeige: 4 - Ausgleichscheibe
unter
dem Meisterritzel zu dünn
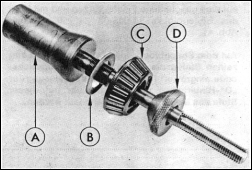
Abb.44 A =
Meisterritzel
B = Neue ausgemessene
Ausgleichscheibe
C = Kegelrollenlager
D = Konusmutter
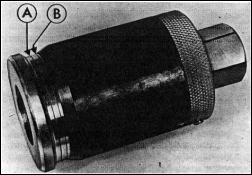
Abb.45
Druckmessgerät 15-023
A = Markierung für neue Lager
B = Markierung für gelaufene Lager
|
- Messuhr wieder einrichten und,
wie vorher beschrieben (Punkt 21), die Stellung des halben
Ausschlages am Meisterritzel ermitteln. Messuhr zur Seite
schwenken.
- Nullstellung der Messuhr am
Messblock mittels Stufenblock wieder prüfen, Abb.46, und
Messblock auf die Stirnfläche des Meisterritzels setzen. Wird
jetzt mit dem Taststift der Messuhr wie vorher (Punkt 23) quer
über die Messwelle gefahren, so muss der Zeiger "0"
anzeigen, wenn die vorausgegangenen Messungen genau waren.
Abweichungen von höchstens 0,01 mm von der "0" sind
zulässig, Abb.47.
Werden trotzdem höhere Abweichungen von der "0"
angezeigt, wie folgt verfahren:
Anzeige rechts von der "0",
eine um den Betrag dickere -
Anzeige links von der "0",
eine um den Betrag dünnere
Ausgleichscheibe einbauen.
Es muss also eine neue Ausgleichscheibe ausgemessen, und der
Kontrollvorgang wiederholt werden, bis eine Abweichung von max.
0,01 mm zur "0"-Stellung gemessen werden.
- Meisterritzel und Messwelle
ausbauen. Ausgemessene Ausgleichscheibe mit Kegelrollenlager vom
Meisterritzel entfernen und auf das einzubauende
Antriebskegelrad schieben. Kegelrollenlager mit dem
Spezialwerkzeug 15-042 aufpressen, Abb.48.
|
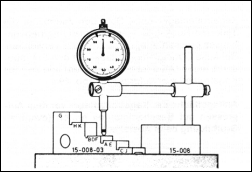
Abb.46 Messuhr
auf "0" stellen
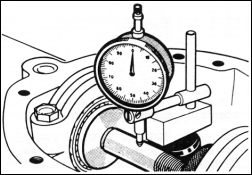
Abb.47
Messuhrstellung "0"
(Abweichung max. 0,01 mm)
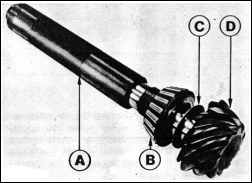
Abb.48 A =
Aufpressdorn 15-042
B = Kegelrollenlager
C = Ausgemessene
Ausgleichscheibe
D = Antriebskegelrad
|
Messung des Gesamtspiels
- Kegelrollenlager ohne Scheiben
zuerst auf die Tellerrad-Rückseite des
Ausgleichgetriebegehäuses pressen. Aufpressdorn 15-025
verwenden. Gehäuse Ausgleichgetriebe auf den Schraubstock legen
(Alubacken verwenden) und zweites Kegelrollenlager aufpressen,
Abb.49.
Auflagefläche der Kegelrollenlager vor dem Aufpressen auf
Beschädigungen prüfen (eventuell Gratbildung beim Abziehen).
- Druckstücke für Druckspindel
15-021 in die Achsrohre einlegen und Ausgleichgetriebe mit
Lagerlaufringen einsetzen, Abb.50.
Lagerdeckel aufsetzen (Zahl zu Zahl) und Schrauben festziehen.
Dann Schrauben wieder lösen und mit dem Schlüssel auf leichten
Anschlag bringen.
- Druckspindel 15-021,
gleichgültig in welchem Achsrohr, einsetzen und mit 5 Nm (50
kpcm) festziehen. Ausgleichgetriebe mehrmals drehen und mit dem
Drehmomentschlüssel nochmals den Wert von 5 Nm (50 kpcm) an der
Druckspindel prüfen, Abb.51.
|
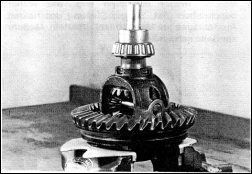
Abb.49
Kegelrollenlager mit Werkzeug 15-031
aufpressen
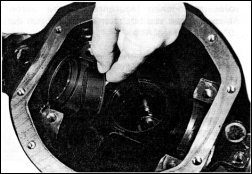
Abb.50
Druckstücke einlegen
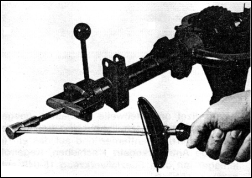
Abb.51
Druckspindel 15-021 einsetzen und
festziehen
|
- Messuhr so am Achsgehäuse
befestigen, dass der Taststift innen am Tellerradbund anliegt
und in der Mitte des Messbereiches der Messuhr auf "0"
steht, Abb.52.
- Druckspindel dann in das andere
Achsrohr setzen und wieder mit 5 Nm (50 kpcm) festziehen.
Je nachdem, von welcher Seite gedrückt wird, läuft der
Messuhrzeiger links oder rechts herum und ist deshalb während
der Messung genau zu beobachten.
Angezeigten Wert an der Uhr ablesen und als Gesamtspiel,
Ausgleichgehäuse im Hinterachsgehäuse, notieren (z.B. 1,35
mm), Abb.53.
- Druckspindel lösen. Messuhr zur
Seite schwenken. Ausgleichgetriebe, Druckspindel und
Druckstücke entfernen.
Bestimmen des Distanzringes
(Antriebskegelrad
Lagervorspannung)
- Messring 15-024 auf das
Antriebskegelrad schieben. Lötdraht von ca. 2 mm Ø zu einem
Ring biegen, der dem Ø des Antriebskegelradschaftes entspricht
und auf den Messring legen, Abb.54.
|
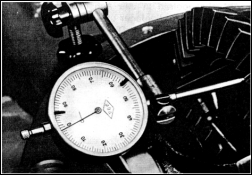
Abb.52 Taststift
der Messuhr auf inneren
Tellerradbund setzen
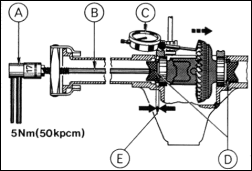
Abb.53 A =
Drehmomentschlüssel
B = Druckspindel 15-021
C = Messuhr
D = Druckstücke
E = Gesamtspiel -
Ausgleichgehäuse im
Hinterachsgehäuse
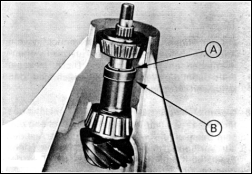
Abb.54 A =
Lötdrahtring
B = Messring 15-024
|
- Antriebskegelrad in das
Achsgehäuse setzen. Kleines Kegelrollenlager und
Flansch-Antriebskegelrad aufschieben. Die noch vom Zerlegen her
aufbewahrte alte selbstsichernde Mutter aufschrauben.
- Flansch-Antriebskegelrad mit dem
Flanschhalter 15-030 festhalten und Mutter langsam festziehen,
Abb.55. Zwischendurch laufend das Durchdrehmoment des
Antriebskegelrades mit der Drehmomentlehre 15-041 prüfen.
Mutter so lange festziehen, bis das gleiche Durchdrehmoment
erreicht ist, das anfangs beim Einbau des Meisterritzels notiert
wurde, z.B. 2,3 Nm (23 kpcm), Abb.56.
Wurde dieses Durchdrehmoment überschritten, muss der
geschilderte Vorgang mit einem neuen Lötdraht wiederholt
werden.
- Zusammengedrückten Lötdraht
vorsichtig vom Antriebskegelrad nehmen und an zwei
gegenüberliegenden Stellen dessen Dicke messen. Falls dabei die
Werte unterschiedlich sind, den Mittelwert errechnen, Abb.57.
- Diesen Messwert (z.B. 1,21 mm)
mit der Höhe des Messringes (9,5 mm) addieren (entsprechend
diesem Beispiel: 9,5 + 1,21 = 10,71 mm). Aus den zur Verfügung
stehenden Distanzringen (siehe Ersatzteil-Katalog) einen Ring
auswählen, der diesem Maß entspricht.
|
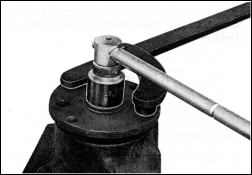
Abb.55 Flansch -
Antriebskegelrad festhalten
und
Mutter langsam festziehen
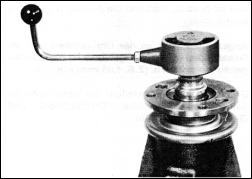
Abb.56
Durchdrehmoment des
Antriebskegelrades
prüfen
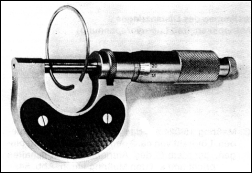
Abb.57 Dicke des
zusammengedrückten
Lötdrahtes
messen
|
Kontrolle
- Antriebskegelrad mit
ausgemessenem Distanzring, kleinem Kugelrollenlager,
Flansch-Antriebskegelrad und alter selbstsichernder Mutter
montieren; Mutter mit vorgeschriebenem Drehmoment festziehen,
Abb.58.
- Antriebskegelrad mehrmals
drehen, dann Durchdrehmoment mit der Drehmomentlehre 15-041
prüfen. Bei diesem Antriebskegelrad z.B. 2,3 Nm (23 kpcm),
Abb.56.
- Wird dieses Durchdrehmoment
nicht erreicht oder überschritten, so muss ein höherer oder
kürzerer Distanzring ausgemessen und anschließend das
Durchdrehmoment wieder geprüft werden.
- Anschließend Mutter und
Flansch-Antriebskegelrad entfernen.
- Neuen Radialdichtring außen
etwas mit Dichtmasse bestreichen und Dichtlippen einfetten (Fett
lt. Spezifikation S-M1C-75A verwenden).
Die Fettfüllung des Anlieferungszustandes muss erhalten
bleiben.
Radialdichtring mit dem Spezialwerkzeug 15-047-A bündig
einpressen, Abb.59.
- Flansch-Antriebskegelrad
aufsetzen. Neue selbstsichernde Mutter mit vorgeschriebenem
Drehmoment festziehen. Das Durchdrehmoment muss sich nach Einbau
des Radialdichtringes und unter Berücksichtigung von dessen
Reibwert (0,2 ... 0,4 Nm / 2 ... 4 kpcm) zwischen 2,5 ... 2,7 Nm
(25 ... 27 kpcm) bewegen.
Ermitteln der Scheiben für
beide Ausgleichgetriebeseiten
- Beide Druckstücke wieder in die
Achsrohre schieben, Abb.60. Ausgleichgetriebe mit
Lageraußenringen in das Achsgehäuse legen. Lagerdeckel
aufsetzen. Schrauben festziehen und wieder lösen, mit dem
Schlüssel auf leichten Anschlag bringen.
|
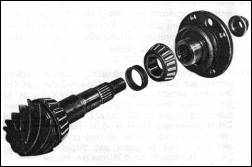
Abb.58
Antriebskegelrad komplett montieren
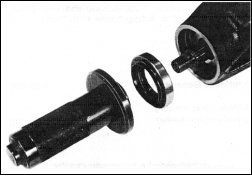
Abb.59
Radialdichtring mit Werkzeug
15-047-A
einpressen
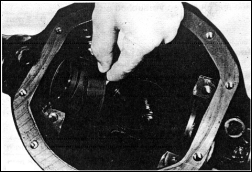
Abb.60
Druckstücke einlegen
|
- Ausgleichgehäuse mit der
Druckspindel vom Antriebskegelrad weg mit 5 Nm (50 kpcm) bis zum
Anschlag drücken. Antriebskegelrad mehrmals durchdrehen.
Drehmoment von 5 Nm (50 kpcm) nochmals prüfen.
- Taststift der Messuhr senkrecht
- d.h. im rechten Winkel zur Zahnflanke - auf einen Zahn des
Tellerrades setzen, Abb.61. Zahnflankenspiel an vier Stellen
messen (Tellerrad um jeweils zwei Schraubenköpfe weiterdrehen).
Abweichungen im Zahnflankenspiel dürfen 0,05 mm nicht
überschreiten. Druckspindel in das andere Achsrohr einführen
und langsam einschrauben, bis ein Zahnflankenspiel von 0,01 mm
gemessen wird.
- Jetzt die Messuhr mit dem
Taststift innen gegen den Tellerradbund setzen, Abb.62. Skala
auf "0" stellen. Danach Druckspindel in das andere
Achsrohr montieren und mit einem Anzugsdrehmoment von 5 Nm (50
kpcm) einschrauben. Messuhrwert ablesen und notieren (z.B.: 0,64
mm), Abb.63. Druckspindel, Ausgleichgetriebe und Druckstücke
aus dem Achsgehäuse entfernen.
Rechenbeispiel
Ermitteltes
Gesamtspiel:
1,35 mm
Mittlere Vorspannung
(grundsätzlich
hinzu)
+ 0,05 mm
1,40 mm
Ausgleichscheibendicke
Tellerradrückseite
Gemessen:
0,64 mm
Erfahrungsgemäß
für Zahnflankenspiel
abziehen: - 0,12 mm
(Dieses Maß ist konstant und
hat sich aus mehreren
Versuchen
ergeben)
0,52 mm
Ausgleichscheibendicke
Tellerradvorderseite
Auf diese Seite des
Ausgleichgetriebes
wird der Rest der Scheiben gelegt.
Gesamtspiel:
1,40 mm
Scheibendicke Tellerradrückseite
abziehen:
- 0,52 mm
0,88 mm
|
Abb.61 Taststift
der Messuhr rechtwinklig auf
einen
Zahn des Tellerrades setzen
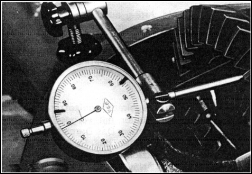
Abb.62 Taststift
der Messuhr auf inneren
Tellerradbund setzen

Abb.63
Ausgleichgehäuse mit Druckspindel
vom
Antriebskegelrad wegdrücken.
Messwert ablesen
|
- Abzieher 15-026 an ein
Kegelrollenlager des Ausgleichgetriebe-Gehäuses setzen und mit
einem Schenkel in den Schraubstock spannen. So beide Lager
abziehen. Bei Verwendung der Grundplatte 370 kann dieser Vorgang
mit Hilfe der Einsätze 15-006 ausgeführt werden, Abb.64.
Auflagefläche der Kegelrollenlager vor dem Aufpressen auf
Beschädigungen prüfen (eventuell Gratbildung beim Abziehen).
- Ausgleichscheiben wie ermittelt
auflegen, Abb.65. Kegelrollenlager zuerst auf die
Tellerradrückseite des Ausgleichgetriebe-Gehäuses pressen
(Aufpressdorn 15-025 verwenden).
- Ausgleichgetriebe-Gehäuse auf
den Schraubstock legen (Alubacken verwenden) und zweites Lager
aufpressen, Abb.66.
|
Abb.64
Kegelrollenlager Ausgleichgetriebe-
Gehäuse
abziehen
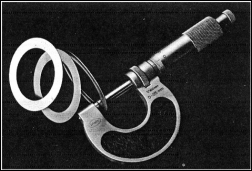
Abb.65 Ermittelte
Ausgleichscheiben
auswählen
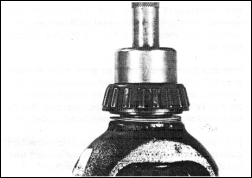
Abb.66
Kegelrollenlager auf Ausgleichgetriebe-
Gehäuse pressen
|
Ausgleichgetriebe einbauen
- Ausgleichgetriebe in
Hinterachsgehäuse drücken. Lagerdeckel aufsetzen (Zahl zu
Zahl). Schrauben mit Dichtmasse einsetzen und mit dem
vorgeschriebenem Drehmoment festziehen, Abb.67.
- Taststift der Messuhr
rechtwinklig auf einen Zahn des Tellerrades setzen und
Zahnflankenspiel messen. Das Zahnflankenspiel muss bei der
"D"-Hinterachse zwischen 0,10 ... 0,20 mm liegen,
Abb.68.
War das Zahnflankenspiel zu groß, müssen Ausgleichscheiben
an der Tellerradvorderseite entnommen und unter das andere
Kegelrollenlager an der Tellerradrückseite gelegt werden. Bei
zu kleinem Zahnflankenspiel umgekehrt verfahren.
Bei diesem Vorgang keine Ausgleichscheiben entfernen oder
zufügen, sondern nur an den Seiten der Kegelrollenlager des
Ausgleichgetriebes tauschen.
|
Abb.67
Lagerdeckel Zahl zu Zahl aufsetzen
und
Schrauben mit vorgeschriebenem
Drehmoment festziehen
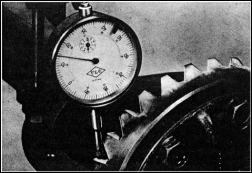
Abb.68 Taststift
der Messuhr rechtwinklig auf
einen
Zahn des Tellerrades setzen
|
Tragbildkontrolle
Neue Tellerräder zeigen noch vom Probelauf im Werk her das
abzustrebende Tragbild! Zur Tragbildkontrolle, die grundsätzlich
nach dem Einbau von Neuteilen erfolgen muss, Zähne des Tellerrades
mit Tuschierfarbe bestreichen. Schlüssel auf die Flanschmutter des
Antriebskegelrades setzen und Antriebskegelrad so oft in beiden
Richtungen drehen, wie Zähne auf dem Tellerrad sind. Das Tragbild
wird besser sichtbar, wenn das Tellerrad dabei am äußeren Umfang
mit einem Hartholzkeil gebremst wird, Abb.69.
Das Zahnflankenspiel hat großen Einfluss auf das Tragbild. Ist das
Tragbild trotz der eingehaltenen Arbeitsfolge nicht befriedigend, so
darf jetzt nur noch eine Korrektur durch Vergrößern oder
Verkleinern des Zahnflankenspiels innerhalb der Toleranz vorgenommen
werden. Dabei keine Ausgleichscheiben entfernen oder zufügen,
sondern nur an den Seiten der Kegelrollenlager des
Ausgleichgetriebes tauschen, Abb.70.
0,01 mm Ausgleichscheibendicke ist gleich 0,01 mm
Zahnflankenspiel.
- Achsgehäuse mit neuer Dichtung
und Deckel verschließen, dabei die neuen kleberbeschichteten
Schrauben verwenden. Schrauben mit vorgeschriebenem Drehmoment
festdrehen.
- Bremsträger auf die
Hinterachsseitenwellen schieben und Seitenwellen in die
Achsrohre einsetzen. Schraubenlöcher zueinander ausrichten und
Schrauben mit vorgeschriebenem Drehmoment festziehen, Abb.71.
Vor dem Einsetzen der Seitenwellen, Lageraußenringe oder
Lagersitze in den Achsrohren mit Lithiumfett bestreichen (Fett
laut Spezifikation S-MIC4515A).
- Hinterachse vom Montageständer
abbauen und Bremsrohrleitung montieren.
- Nach dem Einbau der Hinterachse,
vorgeschriebenes Öl einfüllen.
|
Abb.69 Tellerrad
mit einem Hartholzkeil
abbremsen
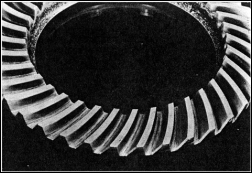
Abb.70
Anzustrebendes Tragbild
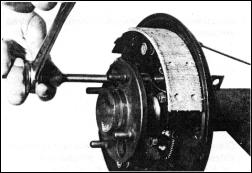
Abb.71 Schrauben
der Seitenwellen festziehen
|
|
15 254
TRÄGER MIT AUSGLEICHGETRIEBE AUS- UND EINBAUEN |
|
KEIN
SPEZIALWERKZEUG ERFORDERLICH
|
|
Ausbauen
- Radmuttern hinten lösen und
Fahrzeug unter den Längsträgern aufbocken.
- Räder abbauen und
Bremstrommeln abziehen.
- Beide Seitenwellen mit
Bremsträger abschrauben (je Seite 4 Schrauben). Wellen aus
der Vielkeilverzahnung des Ausgleichgetriebes herausziehen,
Abb.72.
- Gelenkwelle vom Flansch -
Antriebskegelrad abbauen.
- Ölauffangwanne unter das
Hinterachsgehäuse setzen. Träger mit Ausgleichgetriebe vom
Achsgehäuse abschrauben (8 Muttern), Abb.73.
|
Abb.72
Seitenwelle ausbauen
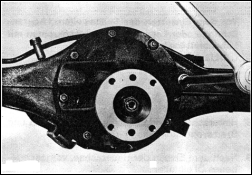
Abb.73
Befestigung - Träger an
Hinterachsgehäuse
|
Einbauen
Dichtflächen an Träger und
Hinterachsgehäuse reinigen, alte Dichtungsreste entfernen.
- Neue Dichtung auflegen,
Träger mit Ausgleichgetriebe an Achsgehäuse montieren und
Muttern mit vorgeschriebenem Drehmoment festziehen, Abb.74.
- Gelenkwelle an Flansch -
Antriebskegelrad anbauen (neue Federringe verwenden).
Schrauben mit vorgeschriebenem Drehmoment festziehen (bei
geteilter Gelenkwelle Einbaufolge in Position
15 514 beachten), Abb.75.
- Seitenwellen einsetzen
(Vielkeilverzahnung), Bremsträger anschrauben. Schrauben mit
vorgeschriebenem Drehmoment anziehen, Abb.76.
- Bremstrommeln und Räder
montieren. Fahrzeug ablassen und Radmuttern festziehen.
- Vorgeschriebenes Öl
einfüllen.
|
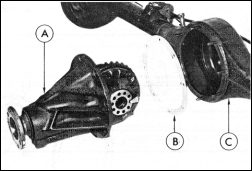
Abb.74 A =
Träger mit Ausgleichgetriebe
B = Dichtung
C = Achsgehäuse
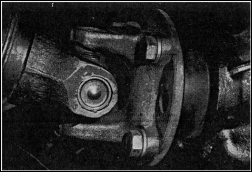
Abb.75
Gelenkwelle an Flansch -
Antriebskegelrad
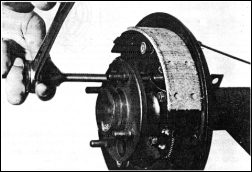
Abb.76
Schrauben der Seitenwelle festziehen
|
"J"-Hinterachse
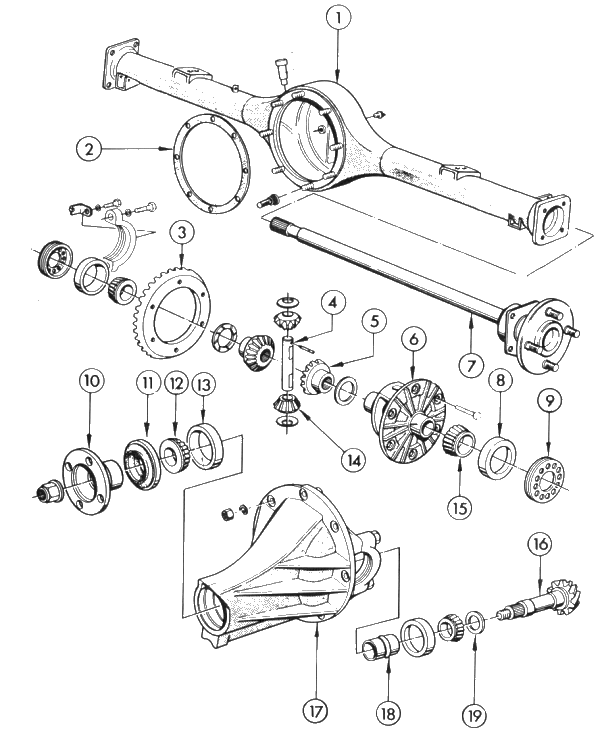
|
Abb.77 1 =
Hinterachsgehäuse
2 = Dichtung
3 = Tellerrad
4 = Welle - Ausgleichkegelräder
5 = Kegelrad - Hinterachswelle
6 = Gehäuse - Ausgleichgetriebe
7 = Hinterachsseitenwelle
8 = Außenlaufring - Kegelrollenlager
9 = Einstellmutter
10 = Flansch - Antriebskegelrad
11 = Radialdichtring
12 = Innenlaufring mit Kegelrollen
13 = Außenlaufring Kegelrollenlager 14 = Ausgleichkegelrad
15 = Innenlaufring mit Kegelrollen 16 = Antriebskegelrad
17 = Träger - Ausgleichgetriebe
18 = Schrumpfhülse Antriebskegelrad
19 = Ausgleichscheibe - Antriebskegelrad
|
|
15 254 8
TRÄGER MIT AUSGLEICHGETRIEBE ZERLEGEN UND ZUSAMMENBAUEN |
|
ERFORDERLICHES
SPEZIALWERKZEUG:
Aufspannvorrichtung
................................
Messblock
...............................................
Stufenblock .............................................
Messwelle ...............................................
Meisterritzel ............................................
Messuhrhalter .........................................
Druckmessgerät ......................................
Abzieher Differentiallager .........................
Flanschhalter ...........................................
Aufpressdorn Differentiallager .................. |
16-009
15-008
15-008-03
15-019
15-020
15-022
15-023
15-026
15-030
15-031 |
|
|
Ausgleichgetriebe und
Antriebskegelrad ausbauen
- Aufspannvorrichtung 16-009
montieren und Träger mit Ausgleichgetriebe in den
Montageständer spannen, Abb.78.
- Sicherungsbleche an den
Ringmuttern entfernen (2 Schrauben).
- Lagerdeckel kennzeichnen und
abschrauben (4 Schrauben). Ausgleichgetriebe mit Ringmuttern
aus dem Gehäuse heben, Abb.79.
|
Abb.78 Träger
mit Ausgleichgetriebe in
Aufspannvorrichtung 16-009 an
Montageständer
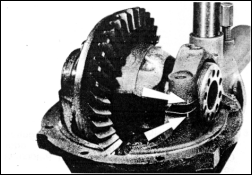
Abb.79
Lagerdeckel kennzeichnen und
abschrauben
|
- Flansch - Antriebskegelrad mit
dem Spezialwerkzeug 15-030 festhalten und Mutter abschrauben,
Abb.80.
- Flansch - Antriebskegelrad mit
dem Abzieher G2-4851-A/6312-A abziehen. Antriebskegelrad
ausbauen (evtl. mit einem Kunststoffhammer aus dem Gehäuse
klopfen), Abb.81.
- Inneres Kegelrollenlager vom
Antriebskegelrad abziehen. Hierzu Abzieher G2-4621-A1 oder
Grundplatte 370 mit den Einsetzen P-4000-28 verwenden, Abb.82.
|
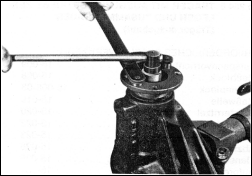
Abb.80 Flansch
- Antriebskegelrad festhalten

Abb.81 Flansch
- Antriebskegelrad abziehen
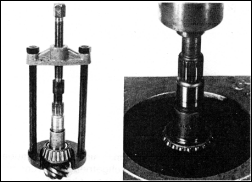
Abb.82
Kegelrollenlager abziehen
|
- Äußeres Kegelrollenlager und
Radialdichtring mit dem Spezialdorn 15-042 gleichzeitig aus
dem Achsgehäuse entfernen, Abb.83.
- Lageraußenring vom äußeren
Kegelrollenlager mit dem Spezialdorn 15-043 heraustreiben und
neuen Lageraußenring mit dem Spezialwerkzeug 15-034
einziehen.
Inneren Lageraußenring auf gleiche Weise erneuern, Abb.84.
Lageraußenringe unbedingt nacheinander auswechseln, damit
jeweils ein Lageraußenring als Führung des Einziehwerkzeuges
dient.
Lagersitze und Anlageflächen müssen frei von Beschädigungen
sein.
|
Abb.83
Äußeres Kegelrollenlager und
Radialdichtring
herausdrücken.
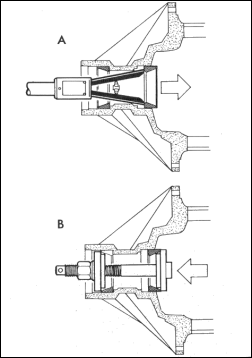
Abb.84 A =
Lageraußenring heraustreiben
B = Lageraußenring einziehen
|
Ausgleichgetriebe
zerlegen
- Abzieher 15-026 an ein
Kegelrollenlager des Ausgleichgetriebe-Gehäuses setzen und
mit einem Schenkel in den Schraubstock spannen. So beide Lager
abziehen, Abb.85.
- Tellerradschrauben
herausdrehen und Tellerrad vom Gehäuse Ausgleichgetriebe
entfernen (6 Schrauben), Abb.86.
Spiel der Achswellenkegelräder einzeln mit einer Fühlerlehre
messen, Abb.87. Liegt das Spiel über dem vorgeschriebenen
max. Wert von 0,15 mm, muss es durch die Montage von neuen
Beilagscheiben (verschiedene Dicken siehe Ersatzteilkatalog)
verringert werden. Liegt das Spiel darunter, ist ein Zerlegen
des Ausgleichgetriebes bei ordnungsgemäßem Zustand der
Ausgleich- und Achswellenkegelräder nicht erforderlich. Somit
entfallen die Punkte 11 bis 14.
|
Abb.85
Kegelrollenlager vom Ausgleich-
Getriebegehäuse abziehen
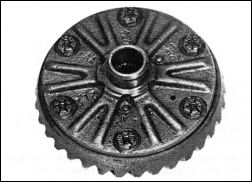
Abb.86
Befestigung Tellerrad an Ausgleich-
Getriebegehäuse
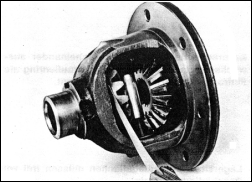
Abb.87 Spiel
der Achswellenkegelräder messen
|
- Spannstift, der die Welle
Ausgleichgetriebe im Gehäuse sichert, mit passendem Dorn
heraustreiben. Welle Ausgleichgetriebe, Ausgleich- und
Achswellenkegelräder ausbauen, Abb.88.
Ausgleichgetriebe
zusammenbauen
- Achswellenkegelräder mit je
einer neuen Beilagscheibe in das Ausgleichgetriebegehäuse
einführen.
Gerillte Seite der Beilagscheiben muss zum
Achswellenkegelrad zeigen, Abb.89.
- Beide Ausgleichkegelräder mit
je einer Druckscheibe gleichzeitig zwischen die
Achswellenkegelräder drehen. Welle einschieben (Bohrung für
Spannstift beachten).
Spiel der Achswellenkegelräder einzeln mit einer Fühlerlehre
prüfen und sicherstellen, dass es nicht über dem max. Wert
von 0,15 mm liegt. Falls erforderlich, Ausgleichgetriebe
wieder zerlegen und stärkere Beilagscheiben einbauen.
- Welle Ausgleichgetriebe mit
einem Spannstift sichern.
- Tellerrad ca. 10 Minuten in
kochendem Wasser erwärmen, zu den Löchern des
Ausgleichgetriebe-Gehäuses ausrichten, neue
Originalschrauben eindrehen und mit vorgeschriebenem
Drehmoment festziehen, Abb.90.
|
Abb.88
Spannstift Ausgleichgetriebewelle
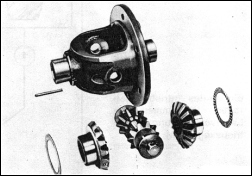
Abb.89
Ausgleichgetriebe zerlegt
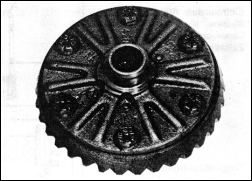
Abb.90
Befestigung Tellerrad an Ausgleich-
Getriebegehäuse
|
Allgemeines
über die Einstellung von Teller- und Antriebskegelrad
- Teller- und Antriebskegelrad
bilden grundsätzlich eine Einheit und dürfen nicht einzeln
verwendet werden.
- Das im Text genannte
Spezialwerkzeug ist für die einzelnen Vorgänge
unerlässlich.
- Es ist auf unbedingte
Sauberkeit und Messgenauigkeit zu achten.
- Alte Lager- und Gleitstellen
sind beim Einbau mit dem vorgeschriebenen Hypoidöl
einzuölen.
- Die Innenteile einer komplett
eingestellten Achse können nicht ohne Einstell- und
Messvorgänge in ein anderes, gleiches Achsgehäuse eingebaut
werden.
Die Reihenfolge der Einstell- und
Messvorgänge ist unbedingt einzuhalten:
- Ermitteln der
Ausgleichscheibendicke für Antriebskegelrad.
- Einbau des
Antriebskegelrades (Bestimmen der Lagervorspannung
Antriebskegelrad).
- Einbau des
Ausgleichgetriebes (Bestimmen der Lagervorspannung und des
Zahnflankenspieles).
- Tragbildkontrolle.
a = Druckseite (Zug)
b = Schubseite
|
Abb.91
|
|
Ermitteln der
Ausgleichscheibendicke für Antriebskegelrad
- Das Ermitteln der Scheibendicke
und die damit zusammenhängenden Einstellarbeiten entsprechen
denen der "D"-Hinterachse Position
15 214 8, Punkt 15 bis 29.
Folgende Unterschiede müssen jedoch berücksichtigt werden:
Die zum Einbau vorgesehenen Lager mit beiden Einstellmuttern
(Ringmuttern) auf die Messwelle 15-019 drücken und so in das
Gehäuse einlegen, dass beide Einstellmuttern mit dem Gehäuse
außen fast bündig sind. Wenn nötig, Stellmutter der Messwelle
in ihrer Stellung etwas verändern, Abb.92. Einstellmuttern
leicht beidrehen (bis zur Anlage an die Lageraußenringe).
Beide Lagerdeckel aufsetzen (auf Kennzeichnung achten) und die
Schrauben fingerfest beidrehen. Dabei darauf achten, dass sie
Lagerdeckel voll zur Anlage kommen (Einstellmuttern im richtigen
Gewindeeingriff). Schrauben mit vorgeschriebenem Drehmoment
festziehen, Abb.93.
|
Abb.92 Messwelle
einlegen

Abb.93
Lagerdeckel aufsetzen, dabei auf
korrekte
Anlage der Deckel achten
(Pfeil)
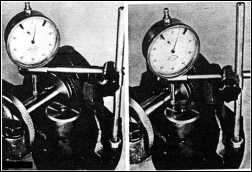
Abb.94 Messwelle
und Meisterritzel justieren
|
Einbau des Antriebskegelrades
(Bestimmen der
Lagervorspannung)
- Antriebskegelrad mit neuer
Schrumpfhülse in das Trägergehäuse einsetzen und äußeres
Kegelrollenlager aufschieben, Abb.95.
- Neuen Radialdichtring außen
etwas mit Dichtmasse bestreichen und Dichtlippen einfetten (Fett
lt. Spezifikation S-MIC75A verwenden).
Die Fettfüllung des Anlieferungszustandes muss erhalten
bleiben.
Radialdichtring mit dem Spezialwerkzeug G2-4676B/P-4129-B
bündig einpressen, Abb.96.
- Flansch Antriebskegelrad
aufsetzen und neue selbstsichernde Mutter aufschrauben.
Flansch mit dem Flanschhalter 15-030 festhalten und Mutter
langsam festziehen, Abb.97.
|
Abb.95
Antriebskegelrad mit Kegelrollenlager
und
Schrumpfhülse
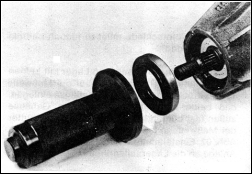
Abb.96
Radialdichtring mit Werkzeug
G2-4676B
einpressen
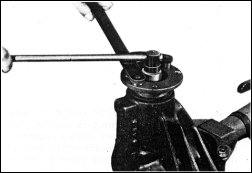
Abb.97 Flansch
Antriebskegelrad festhalten
und
Mutter langsam festziehen
|
Zwischendurch laufend das
Durchdrehmoment des Antriebskegelrades mit der Drehmomentlehre
15-041 prüfen, Abb.98. Mutter so lange festziehen, bis das gleiche
Durchdrehmoment erreicht ist, das anfangs beim Einbau des
Meisterritzels (Position 15 214 8, Punkt 17)
notiert wurde. Bei diesem Antriebskegelrad z.B. 2,3 Nm (23 kpcm).
Das Durchdrehmoment muss sich somit nach Einbau des
Radialdichtringes und unter Berücksichtigung von dessen Reibwert
(0,2 ... 0,4 Nm / 2 ... 4 kpcm) zwischen 2,5 ... 2,7 Nm (25 ... 27
kpcm) bewegen.
Wurde dieses Drehmoment überschritten, muss das Antriebskegelrad
wieder ausgebaut und der geschilderte Vorgang mit einer neuen
Schrumpfhülse wiederholt werden.
Einbau des Ausgleichgetriebes
(Bestimmen der Lagervorspannung
und des Zahnflankenspieles)
- Beide Kegelrollenlager unter
Verwendung des Spezialwerkzeuges 15-031 aufpressen.
Kegelrollenlager zuerst auf die Tellerradrückseite des
Ausgleichgetriebe-Gehäuses pressen. Anschließend Gehäuse auf
den Schraubstock legen (Alubacken verwenden) und zweites Lager
aufpressen, Abb.99.
Lagersitze und Anlageflächen müssen frei von
Beschädigungen sein.
- Komplettes Ausgleichgetriebe mit
Lageraußenringen in das Trägergehäuse legen. Einstellmuttern
dicht neben die Lager in die Gewindegänge stellen, Abb.100.
Einstellmuttern bis zur Anlage an die Lageraußenringe
beidrehen.
- Beide Lagerdeckel aufsetzen (auf
Kennzeichnung achten) und Schrauben mit vorgeschriebenem
Drehmoment festziehen. Anschließend Schrauben wieder lösen und
fingerfest beidrehen. Dabei darauf achten, dass die Lagerdeckel
voll zur Anlage kommen (Einstellmutter im richtigen
Gewindeeingriff).
|
Abb.98
Durchdrehmoment des Antriebs-
Kegelrades
prüfen
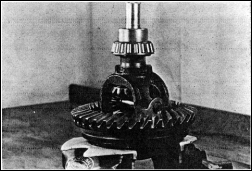
Abb.99
Kegelrollenlager mit Werkzeug
15-031
aufpressen
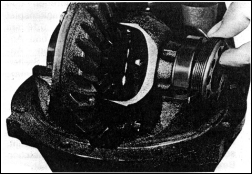
Abb.100
Ausgleichgetriebe mit Ringmuttern
in das Trägergehäuse einsetzen
|
- Messuhr 15-046 mit Halter 15-022
so am Trägergehäuse anbringen, dass der Taststift der Messuhr
senkrecht, d.h. im rechten Winkel zur Zahnflanke, auf einem Zahn
des Tellerrades steht, Abb.101.
- Einstellmutter A mit Werkzeug
15-030 so weit hineinschrauben, bis ein Zahnflankenspiel von
0,01 mm gemessen wird (Einstellmutter B entsprechend lösen),
Abb.102.
- Einstellmutter B langsam
hineindrehen und Zahnflankenspiel messen. Das Zahnflankenspiel
muss bei der "J"-Hinterachse zwischen 0,13 ... 0,18 mm
liegen. Messuhr zur Seite schwenken und Antriebskegelrad
mehrmals durchdrehen. Anschließend Zahnflankenspiel an drei
Stellen nochmals prüfen. Eine Abweichung von max. 0,03 mm ist
zulässig, Abb.103.
Bei einer Korrektur des Zahnflankenspieles müssen die
Einstellmuttern gleichmäßig verstellt werden, damit die
Lagervorspannung nicht verändert wird. Wird z.B. eine Mutter
herausgedreht, so muss die andere Mutter um den gleichen Betrag
hereingedreht werden und umgekehrt.
|
Abb.101 Taststift der
Messuhr rechtwinklig
auf einen Zahn des Tellerrades setzen
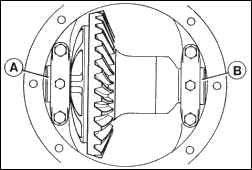
Abb.102 A =
Einstellmutter Tellerradrückseite
B = Einstellmutter Tellerrad-
Vorderseite
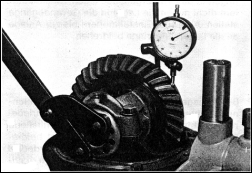
Abb.103
Zahnflankenspiel einstellen
|
- Schrauben der Lagerdeckel mit
vorgeschriebenem Drehmoment festziehen. Messuhr mit Halter
entfernen.
Tragbildkontrolle
Neue Tellerräder zeigen noch vom
Probelauf im Werk her das anzustrebende Tragbild! Zur
Tragbildkontrolle, die grundsätzlich nach dem Einbau von Neuteilen
erfolgen muss, Zähne des Tellerrades mit Tuschierfarbe bestreichen.
Schlüssel auf die Flanschmutter des Antriebskegelrades setzen und
Antriebskegelrad so oft in beiden Richtungen drehen, wie Zähne auf
dem Tellerrad sind. Das Tragbild wird besser sichtbar, wenn das
Tellerrad dabei am äußeren Umfang mit einem Hartholzkeil gebremst
wird, Abb.104.
Das Zahnflankenspiel hat großen Einfluss auf das Tragbild. Ist das
Tragbild trotz der eingehaltenen Arbeitsfolge nicht befriedigend, so
darf jetzt nur noch eine Korrektur durch Vergrößern oder
Verkleinern des Zahnflankenspiels innerhalb der Toleranz vorgenommen
werden. Dabei müssen die Einstellmuttern gleichmäßig verstellt
werden, Abb.105.
- Sicherungsbleche für beide
Ringmuttern montieren und Schrauben mit vorgeschriebenem
Drehmoment festziehen, Abb.106.
- Träger mit Ausgleichgetriebe
vom Montageständer abbauen.
- Nach dem Einbau des Trägers
vorgeschriebenes Öl einfüllen.
|
Abb.104 Tellerrad mit
einem Hartholzkeil
abbremsen
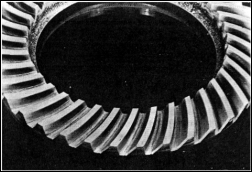
Abb.105 Anzustrebendes
Tragbild
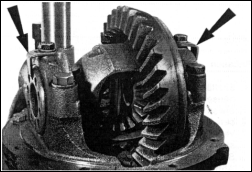
Abb.106 Ringmuttern
sichern
|
|
15 302
RADIALDICHTRING ANTRIEBSKEGELRAD AUSWECHSELN - "D"-ACHSE |
|
ERFORDERLICHE
SPEZIALWERKZEUGE:
Flanschhalter
...........................................
Einbaudorn Dichtring ................................
Auszieher Dichtring ..................................
Flanschabzieher .......................................
|
15-030
15-047-A
15-048
G2-4851-A
/6312-A |
|
|
Ausbauen
- Gelenkwelle vom Flansch
Antriebskegelrad abbauen (4 Schrauben). Anschließend Flansch
Antriebskegelrad mit Spezialwerkzeug 15-030 festhalten und
Mutter abschrauben.
- Ölauffangwanne unter das
Hinterachsgehäuse setzen und Flansch mit Werkzeug
G2-4851-A/6312-A abziehen, Abb.107.
- Achsgehäuse im Bereich des
Radialdichtringes säubern und Dichtring mit Spezialauszieher
15-048 ausbauen: Nach Herausdrehen der mittleren Spindel
Abzieher zwischen Antriebskegelrad und Dichtring bis zum
Kegelrollenlager schieben, damit die Krallen der seitlich
schwenkbaren Arme unter den Radialdichtring fassen können.
Dann die seitliche Spannschraube hineindrehen, bis die Arme
fest am Dichtring anliegen. Dichtring durch Hereindrehen der
mittleren Spindel herausziehen, Abb.108.
Einbauen
- Sitzfläche des
Radialdichtringes im Achsgehäuse reinigen. Neuen
Radialdichtring außen etwas mit Dichtmasse bestreichen und
Dichtlippen einfetten (Fett lt. Spezifikation S-MIC75A
verwenden. Die Fettfüllung des Anlieferungszustandes muss
erhalten bleiben. Dichtring mit dem Spezialwerkzeug
15-047-A bündig einpressen, Abb.109.
|
Abb.107 Flansch
Antriebskegelrad abziehen
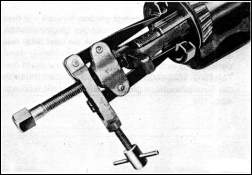
Abb.108 Radialdichtring
mit Werkzeug 15-048
herausziehen
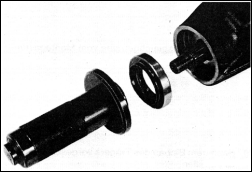
Abb.109 Radialdichtring
mit Werkzeug
15-047-A einpressen
|
Einbauen
- Flansch Antriebskegelrad
aufschieben und neue selbstsichernde Mutter aufschrauben.
Flansch mit Werkzeug 15-030 festhalten und Mutter mit
vorgeschriebenem Drehmoment festziehen, Abb.110.
- Gelenkwelle an Flansch
Antriebskegelrad montieren (neue Federringe verwenden).
Schrauben mit vorgeschriebenem Drehmoment festziehen, Abb.111.
- Ölstand kontrollieren, ggf.
Öl nachfüllen.
|
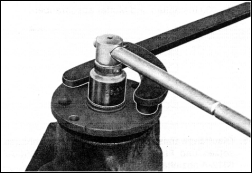
Abb.110 Flansch
Antriebskegelrad festhalten
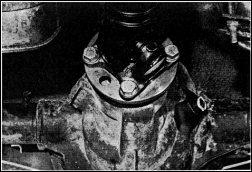
Abb.111 Gelenkwelle
an Flansch Antriebs-
Kegelrad
|
|
15 302
RADIALDICHTRING ANTRIEBSKEGELRAD AUSWECHSELN - "J"-ACHSE |
|
ERFORDERLICHE
SPEZIALWERKZEUGE:
Flanschhalter
...........................................
Drehmomentlehre ...................................
Auszieher Dichtring ..................................
Einbaudorn Dichtring ................................
Flanschabzieher .......................................
|
15-030
15-041
15-048
G2-4676-B
/P-4129-B
G2-4851-A
/6312-A |
|
|
Ausbauen
- Fahrzeug hinten anheben und
unter den Längsträgern aufbocken. Räder und Bremstrommeln
abbauen.
- Gelenkwelle vom Flansch
Antriebskegelrad abbauen (4 Schrauben).
- Drehmomentlehre 15-041 auf die
Flanschmutter setzen und das Gesamtdurchdrehmoment der Achse
messen. Hierzu das Antriebskegelrad gleichmäßig durchdrehen;
Drehmoment ablesen und notieren, z.B. 1,8 Nm (18 kpcm),
Abb.112.
|
Abb.112 Gesamtdurchdrehmoment
der Achse
mit Drehmomentlehre 15-041 messen
(Bremstrommel abgebaut)
|
- Flansch Antriebskegelrad mit
Spezialwerkzeug 15-030 festhalten und Mutter abschrauben.
- Ölauffangwanne unter das
Hinterachsgehäuse setzen und Flansch mit Werkzeug
G2-4851-A/6312-A abziehen, Abb.113.
- Achsgehäuse im Bereich des
Radialdichtringes säubern und Dichtring mit Spezialauszieher
15-048 ausbauen: Nach Herausdrehen der mittleren Spindel
Abzieher zwischen Antriebskegelrad und Dichtring bis zum
Kegelrollenlager schieben, damit die Krallen der seitlich
schwenkbaren Arme unter den Radialdichtring fassen können.
Dann die seitliche Spannschraube hineindrehen, bis die Arme
fest am Dichtring anliegen. Dichtring durch hereindrehen der
mittleren Spindel herausziehen, Abb.114.
Einbauen
- Sitzfläche des
Radialdichtringes im Achsgehäuse reinigen. Neuen
Radialdichtring außen etwas mit Dichtmasse bestreichen und
Dichtlippen einfetten (Fett lt. Spezifikation S-MIC75A
verwenden). Die Fettfüllung des Anlieferungszustandes muss
erhalten bleiben. Dichtring mit dem Spezialwerkzeug
G2-4676-B/P-4129-B bündig einpressen, Abb.115.
|
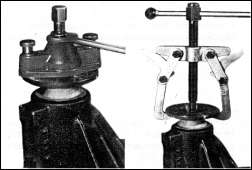
Abb.113 Flansch
Antriebskegelrad abziehen
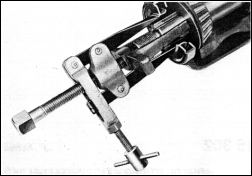
Abb.114 Radialdichtring
mit Werkzeug
15-048 herausziehen
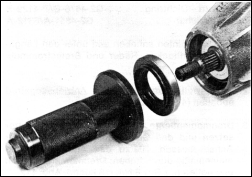
Abb.115 Radialdichtring
mit Werkzeug
G2-4676-B/P-4129-B einpressen
|
- Flansch Antriebskegelrad
aufschieben und neue selbstsichernde Mutter
aufschrauben. Flansch mit Werkzeug 15-030 festhalten, Abb.116,
und Mutter langsam festdrehen, dabei laufend das
Durchdrehmoment des Antriebskegelrades mit der Drehmomentlehre
15-041 prüfen. Mutter so lange festziehen, bis das anfangs
unter Punkt 3 ermittelte Durchdrehmoment zuzüglich 0,2 ...
0,4 Nm (2 ... 4 kpcm) für den Reibwert des Radialdichtringes
erreicht ist, Abb.117.
Beispiel:
vorher ermittelter Wert (Pkt.3) 1,8 Nm
+ Reibwert Radialdichtring
0,2 ... 0,4
Nm
erforderliches Drehmoment
2,0 ... 2,2 Nm
Nach erreichen dieses Wertes, Mutter keinesfalls mehr
zurückdrehen. Wird das Drehmoment überschritten, muss eine
neue Schrumpfhülse eingebaut werden.
- Gelenkwelle an Flansch
Antriebskegelrad montieren (neue Federringe verwenden).
Schrauben mit vorgeschriebenem Drehmoment festziehen, Abb.118.
- Bremstrommeln und Räder
montieren, Fahrzeug ablassen. Ölstand kontrollieren, ggf. Öl
nachfüllen.
|
Abb.116 Flansch
Antriebskegelrad festhalten
und Mutter langsam festziehen
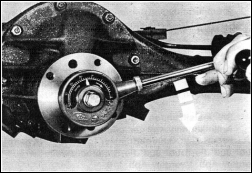
Abb.117
Durchdrehmoment der Achse am
Antriebskegelrad prüfen
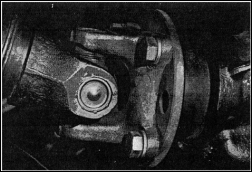
Abb.118 Gelenkwelle
an Flansch Antriebs-
Kegelrad
|
|
15 325
KUGELLAGER - HINTERACHSWELLE AUSWECHSELN |
|
ERFORDERLICHE
SPEZIALWERKZEUGE:
Auf- und
Abzieher Kugellager ...................
Zusatzstück für G1-1225 .........................
Zusatzstück für G1-1225 .........................
Grundplatte ............................................
Einsatz für Grundplatte ............................
Einsatz für Grundplatte ............................ |
G1-1225
G2-1225-A1
G2-1225-B1
370
P-4090-2
P-4090-6 |
|
|
Ausbauen
- Radmuttern lösen, Fahrzeug
hinten anheben und unter den Längsträgern aufbocken. Rad
abbauen.
- Bremstrommel abziehen
(Handbremse gelöst).
- Durch die Montagebohrungen im
Hinterachswellenflansch 4 Schrauben der Halteplatte
abschrauben und Hinterachswelle herausziehen.
Bei festsitzenden Kugellagern der Hinterachswelle können zwei
geeignete Schrauben von hinten in den Achsrohrflansch
(gegenüberliegend) eingeschraubt und die Hinterachswelle
herausgedrückt werden, Abb.119.
- Kugellager Haltering mit einem
8 mm Bohrer anbohren und entfernen bzw. Haltering auflegen und
diesen mit einem Meißel mehrmals auf der gleichen Stelle
anschlagen, bis er von Hand abgenommen werden kann, Abb.120.
- Werkzeug G1-1225 in den
Schraubstock spannen. Ausbauring G2-1225-A1 mit
Hinterachswelle in das Werkzeug montieren und Kugellager
abdrücken, dabei die Spindel des Werkzeuges entgegen dem
Uhrzeigersinn drehen, Abb.121. Bei Benutzung der Grundplatte,
Zusatzstück P-4090-6 verwenden.
|
Abb.119 Hinterachswelle
mit zwei geeigneten
Schrauben herausdrücken
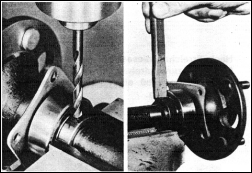
Abb.120 Kugellager
Haltering entfernen
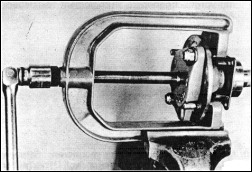
Abb.121 Kugellager
von der Welle abdrücken
|
Einbauen
- Hinterachswellen Halteplatte,
neues Kugellager (Dichtring im Kugellager - dem
Hinterachswellenflansch entgegengesetzt) und neuen Haltering
auf die Hinterachswelle schieben.
- Hinterachswelle
einschließlich Einbauring G2-1225-B1 bzw. Zusatzstück
P-4090-2 in das Werkzeug montieren und Kugellager mit
Haltering aufziehen, Abb.122.
Vor der Montage der Hinterachswelle Lageraußenring oder
Lagersitz im Achsrohr mit Lithiumfett bestreichen (Fett lt.
Spezifikation S-MIC4515A).
- Hinterachswelle in das
Achsrohr einsetzen (auf korrekten Sitz des Bremsträgers
achten) und Schrauben der Halteplatte mit vorgeschriebenem
Drehmoment festziehen, Abb.123.
- Bremstrommel und Rad
montieren. Fahrzeug ablassen und Radmuttern festziehen.
- Ölstand im Hinterachsgehäuse
prüfen, ggf. Öl nachfüllen.
|
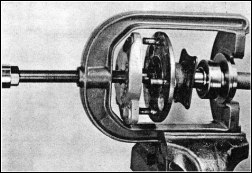
Abb.122 Kugellager
auf die Welle ziehen
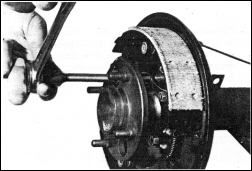
Abb.123 Schrauben der
Hinterachswelle
festziehen
|
|
15 441
RADBOLZEN HINTEN AUSWECHSELN |
|
KEIN SPEZIALWERKZEUG
ERFORDERLICH
|
|
- Rad und Bremstrommel abbauen.
Rändelverzahnte Radbolzen aus dem Radnabenflansch treiben.
Neue Radbolzen mittels einer Radmutter und passenden
Unterlegscheiben in den Flansch einziehen. Bremstrommel und
Rad montieren, Abb.124.
|
Abb.124 Radbolzen in
den Flansch einziehen
|
|
15 514
GELENKWELLE KOMPLETT AUS- UND EINBAUEN |
|
KEIN SPEZIALWERKZEUG
ERFORDERLICH
|
|
Ausbauen
- Gelenkwelle vom Flansch
Antriebskegelrad abbauen (4 Schrauben), Abb.125.
- Bei geteilter Gelenkwelle
Mittellager abschrauben (2 Schrauben), Abb.125.
Sind zwischen Mittellagergehäuse und Bodengruppe
Distanzscheiben eingebaut, müssen diese beim Einbau der
Gelenkwelle wieder beigelegt werden, da sonst der vordere und
hintere Teil der Gelenkwelle im falschen Winkel zueinander
stehen.
- Gelenkwelle komplett aus der
Getriebeverlängerung ziehen. Damit kein Getriebeöl
ausläuft, alten Gelenkwellenstummel bzw. Schutzkappe
Hauptwelle in die Getriebeverlängerung schieben, Abb.126.
Einbauen
- Gelenkwellenstummel bzw.
Schutzkappe Hauptwelle entfernen.
- Gelenkwelle vorsichtig in die
Getriebeverlängerung einschieben, ohne den Dichtring zu
beschädigen.
- Gelenkwellenmittellager (bei
geteilter Gelenkwelle) mit den beiden Befestigungsschrauben lose
am Bodenblech vormontieren.
Evtl. vorhandene Distanzscheiben wieder zwischen
Mittellagergehäuse und Bodengruppe einsetzen.
|
Abb.125 A =
Befestigung Mittellager an
Bodengruppe
B = Gelenkwelle an Flansch
Antriebskegelrad
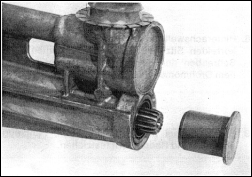
Abb.126 Schutzkappe
für Getriebehauptwelle

Abb.127 A =
einteilige Gelenkwelle
B = geteilte Gelenkwelle
|
- Gelenkwelle an Flansch
Antriebskegelrad montieren (neue Federringe verwenden).
Schrauben mit vorgeschriebenem Drehmoment festziehen.
- Mittellager parallel zur
Gelenkwelle und spannungsfrei mit vorgeschriebenem Drehmoment
festziehen, Abb.128.
|
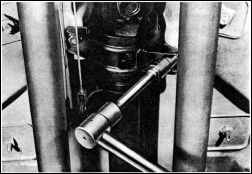
Abb.128 Mittellagerschrauben
|
- Bei Gelenkwellen mit
Gleichlaufschiebegelenk (Löbro-Gelenk), Fahrzeug hinten
anheben, so dass die Hinterachse frei nach unten hängen
kann.
- Vorderen Teil der Gelenkwelle einschließlich
Mittellager so weit nach vorn in Richtung Getriebe ziehen,
bis im Gleichlaufschiebegelenk hinter dem Mittellager eine
metallische Anlage zu spüren ist.
|
- In dieser Lage der Gelenkwelle
mit Gleichlaufschiebegelenk, sind die beiden
Befestigungsschrauben des Mittellagers mit vorgeschriebenem
Drehmoment festzuziehen. Hierbei ist außerdem darauf zu
achten, dass das Mittellagergehäuse parallel zur
Gelenkwelle festgeschraubt wird.
- Eventuell verlorengegangenes
Getriebeöl ergänzen.
|
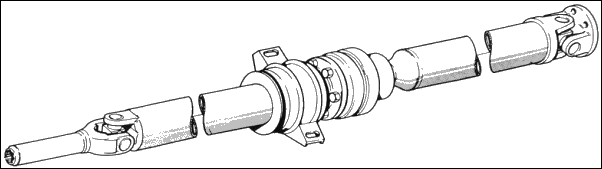 |
Abb.129 Gelenkwelle
mit Gleichlaufschiebegelenk
|
|
|
15 564 4
KUGELLAGER GELENKWELLE AUSWECHSELN |
|
KEIN SPEZIALWERKZEUG
ERFORDERLICH
|
|
Ausbauen
- Sicherungsblech aufbiegen.
- Schraube am Gabelstück lösen
und U-Schraube seitlich herausnehmen.
- Gelenkwelle trennen und
Gummilager mit Gehäuse vom Kugellager abheben.
- Gummilager aus dem Gehäuse
herausnehmen.
- Kugellager, zusammen mit den
Schutzkappen, mit einem zweiarmigen Abzieher von der Welle
abziehen, Abb.130.
Einbauen
- Hohlräume zwischen Kugellager
und Schutzkappen mit Fett lt. Spezifikation S-MIC4515-A
füllen und Kugellager samt Schutzkappen mit einem geeigneten
Rohrstück auf die Welle treiben.
- Die sechs Blechzungen am
Gehäuse etwas nach außen biegen und Gummilager einsetzen.
Die Warze am Gummilager (Abb.131, Pfeil A) muss in
Einbaulage oben stehen.
- Blechzungen mit einer
Wasserpumpenzange über die Gummiwulst zurückbiegen, Abb.132.
|
Abb.130 Kugellager
mit Schutzkappen abziehen

Abb.131 A =
Markierung für Einbaulage oben
1 = Gummilager
2 = Gehäuse
3 = Blechsicherung
4 = Schraube
5 = Schutzkappe
6 = Kugellager
7 = Schutzkappe
8 = Gabelkopf
9 = U-Scheibe
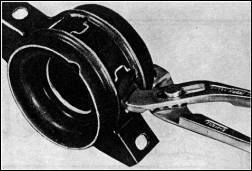
Abb.132 Blechzungen
(6) über die Gummiwulst
biegen
|
- Gehäuse mit Gummilager über
das Kugellager schieben.
Die halbrunde Ausnehmung am äußeren Rand des Gehäuses muss
in Fahrtrichtung zeigen, Abb.133.
- Schraube mit Sicherungsblech
so weit in die vordere Gelenkwelle einschrauben, dass die
U-Scheibe sich noch einschieben lässt.
- Beide Gelenkwellen
zusammensetzen.
Um Unwucht zu vermeiden, Gelenkwellen in ursprünglicher
Stellung zueinander montieren (Markierung bzw. Doppelzahn
beachten!), Abb.134.
- U-Scheibe mit dem Zapfen zur
Verzahnung hin einschieben, Abb.135.
- Schraube festziehen und
sichern.
|
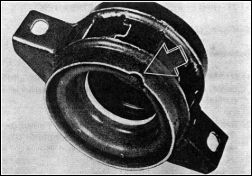
Abb.133 Gehäusemarkierung
(Fahrtrichtung)
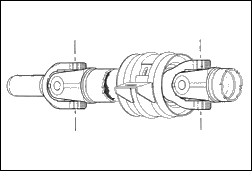
Abb.134 Einbaulage -
vorderer und hinterer
Gelenkwellenstrang
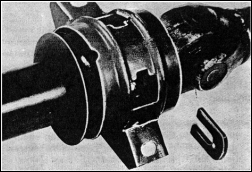
Abb.135 U-Scheibe
einsetzen
|
|
15 621
HINTERFEDER AUS- UND EINBAUEN |
|
KEIN SPEZIALWERKZEUG
ERFORDERLICH
|
|
Ausbauen
- Radmuttern lösen, Fahrzeug
hinten anheben und unter den Längsträgern aufbocken (Feder
ist entlastet), Rad abbauen.
- Selbstsichernde Muttern (4)
von den Federbügeln abschrauben. Federbügel, Gegenplatte (D)
und Gummilager (C) entfernen, Abb.136.
- Federgehänge ausbauen, hierzu
zwei selbstsichernde Muttern abschrauben und je eine
Federlasche nach rechts und links herausziehen, Abb.137,
Gummilager (B) und Halter Gummilager (A) von der Hinterfeder
abheben, Abb.136.
- Vorderen Federbolzen ausbauen
und, falls erforderlich, Federauge mit einem Schraubendreher
aus dem Federbock drücken. Hinterfeder herausnehmen, Abb.138.
Einbauen
- Vorderes Federende in den
Federbock einführen und Federbolzen von innen nach außen
einführen. Selbstsichernde Mutter noch nicht festziehen,
Abb.138. Gummilager (C) und Halter Gummilager (D) auf die
Feder legen.
|
Abb.136 A = Halter
Gummilager
B = Gummilager oben
C = Gummilager unten
D = Gegenplatte
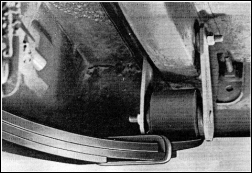
Abb.137
Federaufhängung hinten
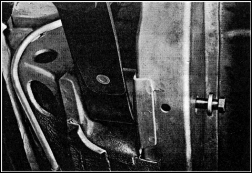
Abb.138
Federaufhängung vorn
|
- Beide Federlaschen montieren,
dabei auf korrekten Sitz der Gummibüchsen im Längsträger
achten. Muttern noch nicht festziehen, Abb.139.
- Unteres Gummilager,
Gegenplatte und Federbügel montieren. Hinterachse mit
Halter und beide Gummilager zum Herzbolzen der Feder
zentrieren. Neue selbstsichernde Muttern auf die
Federbügel schrauben. Hinterachse fest andrücken (evtl.
Feder mit einem Wagenheber etwas anheben) und Muttern
gleichmäßig beidrehen, anschließend mit vorgeschriebenem
Drehmoment festziehen, Abb.140.
- Rad anbauen, Fahrzeug ablassen
und Radmuttern festziehen. Muttern der vorderen und hinteren
Federaufhängung mit vorgeschriebenem Drehmoment festziehen.
Alle Muttern - Hinterfederbefestigung an Bodengruppe -
dürfen nur unter Belastung der Feder, d.h. im eingefederten
Zustand, festgezogen werden.
|
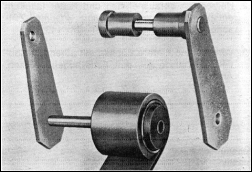
Abb.139 Federlaschen
mit Gummibüchsen
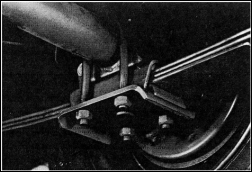
Abb.140 Federbügel
|
|
15 621 8
HINTERFEDER ZERLEGEN UND ZUSAMMENBAUEN |
|
KEIN SPEZIALWERKZEUG
ERFORDERLICH
|
|
Zerlegen
- Feder neben dem Herzbolzen in
den Schraubstock spannen, Federklammern aufbiegen und Mutter
des Herzbolzens abschrauben, Abb.141.
|
Abb.141 Federklammer
und Herzbolzen
|
- Herzbolzen herausnehmen und
Feder langsam entspannen. Federblätter und 4
Gummi-Zwischenlagen auseinanderlegen, Abb.143.
- Vordere und hintere Büchse
mit einem passenden Rohrstück aus den Federaugen pressen,
Abb.142.
Zusammenbauen
- Büchsen mit dem gleichen
Rohrstück in das vordere und hintere Federauge pressen,
Abb.142.
Die Innendurchmesser der vorderen und hinteren Büchsen
sind unterschiedlich (Vorne: 7/16"Ø, hinten:
5/16"Ø).
- Beide Federklammern vom
Federblatt abbauen, dazu Befestigungsniete ausbohren. Neue
Federklammern festnieten.
- Federblätter mit
Gummi-Zwischenlagen in richtiger Reihenfolge aufeinanderlegen
und mit einem entsprechenden Dorn zentrieren, Abb.143 und 144.
- Feder im Schraubstock
zusammendrücken, Herzbolzen einsetzen und Mutter festziehen.
- Federklammer-Unterlagen (2)
auf das Hauptfederblatt legen, Federklammer auf korrekten Sitz
prüfen und umbiegen.
|
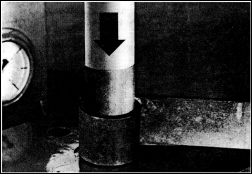
Abb.142 Büchse
Federauge aus- bzw.
einpressen
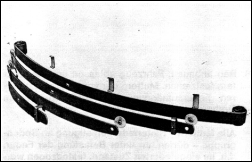
Abb.143 Hinterfeder
zerlegt
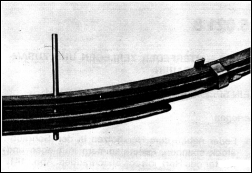
Abb.144 Federblätter
zentrieren und
zusammenbauen
|
|
15 752
STABILISATOR AUS- UND EINBAUEN |
|
KEIN SPEZIALWERKZEUG
ERFORDERLICH
|
|
Ausbauen
- Fahrzeug anheben.
- Beide Haltebügel der
Stabilisatorbefestigung an Hinterachse abschrauben (4
Schrauben). Hierzu den Stabilisator nach hinten ziehen (evtl.
mit einem geeigneten Werkzeug), um die Schrauben spannungsfrei
herausdrehen zu können, Abb.145.
- Stabilisatoraufhängungen am
Längsträger lösen (2 Schrauben mit Muttern), Abb.146.
Stabilisator etwas drehen und nach einer Seite herausnehmen.
Einbauen
- Stabilisator von der Seite her
einsetzen und Schraube - Stabilisator an Längsträger - von
innen nach außen einführen, Abb.146. Unterlegscheiben
aufschieben und selbstsichernde Mutter aufschrauben, jedoch
noch nicht festziehen.
- Haltebügel aufsetzen.
Stabilisator mit Haltebügel und Lagergummis unter Verwendung
eines geeigneten Werkzeuges nach hinten ziehen bzw. auf die
Lagerböcke drücken, damit die Schraubenlöcher zueinander
ausgerichtet sind und die Schrauben spannungsfrei eingedreht
werden können, Abb.145. Schrauben mit vorgeschriebenem
Drehmoment festziehen.
- Fahrzeug ablassen und durch
Belastung (ca. 2 Personen) so weit einfedern, bis die
Achsrohrmitte und die Mitte der hinteren Federaugen in der
gleichen horizontalen Ebene liegen. In dieser Stellung Muttern
- Stabilisator an Längsträger - mit vorgeschriebenem
Drehmoment festziehen, Abb.147.
|
Abb.145 Befestigung -
Stabilisator an
Hinterachse
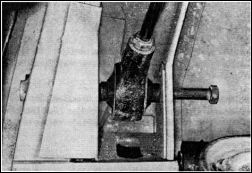
Abb.146 Befestigung -
Stabilisator an
Bodengruppe
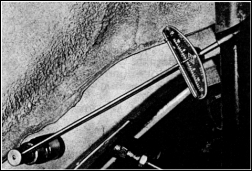
Abb.147 Mutter im
eingefederten Zustand des
Fahrzeuges mit vorgeschriebenem
Drehmoment festziehen.
|
|
15 754 4
GUMMIBÜCHSEN-STABILISATOR AN HINTERACHSE AUSWECHSELN |
|
KEIN SPEZIALWERKZEUG
ERFORDERLICH
|
|
Ausbauen
- Auf einer Seite Kontermutter
lösen und Stabilisatorendstück abschrauben. Sechskantmutter
abschrauben und beide Gummilager vom Stabilisator abziehen,
Abb.148.
Einbauen
- Gummilager mit Glyzerin
einreiben und auf den Stabilisator schieben. Sechskantmutter
und Stabilisatorendstück aufschrauben.
Stabilisatorendstück so weit aufschrauben, bis das in
Abb.149 gezeigte Maß "A" erreicht ist. Die
Maßabweichung zwischen beiden Stabilisatorseiten darf 2,5 mm
nicht überschreiten.
Sechskantmutter kontern, dabei darauf achten, dass die
Mittellinien von Endstückauge und Stabilisatorlängsseite
zueinander parallel verlaufen, Abb.149.
|
Abb.148 A = Endstück
B = Kontermutter
C = Gummilager
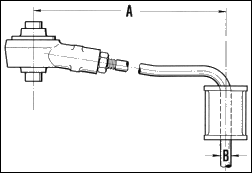
Abb.149 A = 262 ±
2,5 mm
B = 10 mm
|
|
15 756 4
GUMMIBÜCHSE STABILISATOR AN LÄNGSTRÄGER AUSWECHSELN |
|
KEIN
SPEZIALWERKZEUG ERFORDERLICH
|
|
Ausbauen
- Gummibüchse mit einem
geeigneten Rohrstück aus dem Stabilisatorendstück pressen,
Abb.150.
Einbauen
- Gummibüchse mit dem gleichen
Rohrstück so weit einpressen, bis der äußere Stahlmantel
der Büchse mit der Innenseite des Endstückes bündig ist.
Hierbei ist besonders auf die richtige Lage der beiden
halbrunden Aussparungen in der Gummibüchse zu achten,
Abb.151.
|
Abb.150 Gummibüchse
aus dem Endstück
pressen
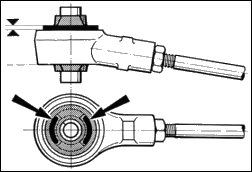
Abb.151 Einbaulage
der Gummibüchsen
|
|
15 791
STOSSDÄMPFER HINTEN AUS- UND EINBAUEN |
|
KEIN
SPEZIALWERKZEUG ERFORDERLICH
|
|
Ausbauen
- Sitzbank ausbauen, dazu 2
Schrauben am Querträger lösen.
- Sicherheitsgurt oben an der
B-Säule abschrauben.
- Abdeckblende der B-Säule
durch Lösen zweier Schrauben entfernen, Abb.152.
- Obere Abdeckblende des
Seitenfensters abbauen (4 Schrauben), Abb.153.
|
Abb.152 Abdeckblende
B-Säule
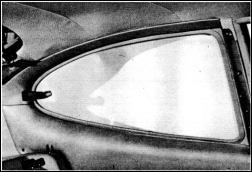
Abb.153 Abdeckblende
Seitenfenster
|
- Zwei Schrauben der
Einstiegleiste am hinteren Ende entfernen und Dichtgummi Tür
im Bereich der Seitenverkleidung abziehen.
- Seitenverkleidung (2
Schrauben) und Teppichboden Kofferraum herausnehmen.
- Abdeckung des Rückwandbleches
(5 Schrauben) und Seitenwand (10 Schrauben) ausbauen, dabei
Rückenlehne umlegen, Abb.154 und 155.
- Stoßdämpfer von Radkasten
und Hinterachse abbauen, Abb.156 und 157.
Einbauen
Vor Einbau der Stoßdämpfer
Dämpfungsgummiringe überprüfen, ggf. erneuern.
- Stoßdämpfer zuerst an der
Hinterachse befestigen. Anschließend Dämpfer
auseinanderziehen und an Radkasten montieren (auf korrekten
Sitz der Gummiringe achten).
- Abdeckung
Seitenwand/Rückwandblech anbringen und Teppichboden
Kofferraum einlegen.
- Seitenverkleidung anbringen,
Dichtungsgummi Tür aufschieben und Einstiegleiste befestigen.
|
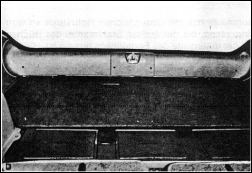
Abb.154 Abdeckung
Rückwandblech
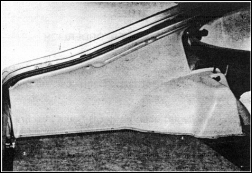
Abb.155 Abdeckung
Seitenwand
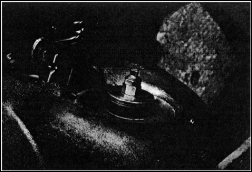
Abb.156 Befestigung
Stoßdämpfer an
Radkasten
|
- Obere Abdeckblende
Seitenfenster und Abdeckblende B-Säule anbringen.
- Sicherheitsgurt an B-Säule
befestigen und Sitzbank einbauen.
|
Abb.157 Befestigung
Stoßdämpfer an
Hinterachse
|
|
15 793
GUMMIRINGE STOSSDÄMPFER AUSWECHSELN |
|
KEIN
SPEZIALWERKZEUG ERFORDERLICH
|
|
Ausbauen
Arbeitsreihenfolge, wie in Position
15 791 von Punkt 1 bis 7 beschrieben, durchführen.
- Kontermuttern Stoßdämpfer an
Radkasten abschrauben, Scheibe und oberen Gummiring abnehmen,
Abb.158.
- Stoßdämpfer zusammendrücken
und unteren Gummiring mit Scheibe entfernen, Abb.159.
Einbauen
- Scheibe und unteren Gummiring,
mit dem Kragen nach oben zeigend, auf die Kolbenstange
schieben. Kolbenstange durch das Aufnahmeloch im Radkasten
führen, Abb.159.
- Oberen Gummiring mit dem
Kragen nach unten zeigend einsetzen, Scheibe auflegen und
Kontermuttern festziehen, Abb.158.
Arbeitsfolge, wie in Position 15 791 von Punkt 10 bis 13
beschrieben, durchführen.
|
Abb.158 Oberer
Gummiring
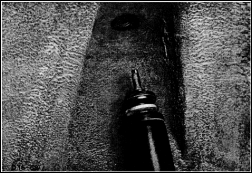
Abb.159 Unterer
Gummiring
|
TECHNISCHE DATEN
Motor |
Getriebe |
Untersetzung |
"D"-Achse |
"J"-Achse |
1,3
HC |
mech. |
- |
4,125
: 1 |
autom. |
- |
- |
1,6
HC |
mech. |
3,75
: 1 |
3,77
: 1 |
autom. |
3,75
: 1 |
3,77
: 1 |
1,6
HC (GT) |
mech. |
3,75
: 1 |
3,77
: 1 |
autom. |
3,75
: 1 |
3,77
: 1 |
2,0
HC |
mech. |
3,44
: 1 |
- |
autom. |
3,44
: 1 |
- |
2,3
HC |
mech. |
3,22
: 1 |
- |
autom. |
3,22
: 1 |
- |
3,0
HC |
mech. |
3,09
: 1 |
- |
autom. |
3,09
: 1 |
- |
|
"D"-Achse |
"J"-Achse |
Zahnflankenspiel |
0,10
... 0,20 mm |
0,127
... 0,178 mm |
Breite
Distanzring |
11,5
... 11,7 mm |
- |
Breite
Schrumpfhülse |
- |
48,7
... 48,9 mm |
Lagervorspannung
Ausgleichgetriebe |
0,03
... 0,10 mm |
0,20
... 0,25 mm |
Ölsorte |
SQM-2C9002AA
(SAE 90) |
Füllmenge |
1,1
Ltr. |
1,14
Ltr. |
Anzugsdrehmomente |
Nm
(kpm) |
|
"D"-Achse |
"J"-Achse |
Lagerdeckel
an Achsgehäuse |
60
... 68 (6,0 ... 6,8) |
62
... 69 (6,2 ... 6,9) |
Deckel
an Achsgehäuse |
35
... 45 (3,5 ... 4,5) |
- |
Träger
Ausgleichgetriebe an Achsgehäuse |
- |
35
... 41 (3,5 ... 4,2) |
Tellerrad
an Ausgleichgetriebegehäuse |
80
... 87 (8,0 ... 8,7) |
69
... 76 (6,9 ... 7,6) |
Mittellager
Gelenkwelle an Bodengruppe |
18
... 23 (1,8 ... 2,3) |
Gelenkwelle
an Flansch Antriebskegelrad |
60
... 65 (6,0 ... 6,5) |
Halteplatte
Seitenwelle an Achsflansch |
27
... 31 (2,7 ... 3,1) |
21
... 25 (2,1 ... 2,5) |
Selbstsichernde
Mutter Antriebskegelrad |
100
... 120 (10,0 ... 12,0) |
- |
Stoßdämpfer
an Hinterachse |
53
... 63 (5,3 ... 6,3) |
Stoßdämpfer
an Bodengruppe |
27
... 33 (2,7 ... 3,3) |
Stabilisator
an Achsrohr |
40
... 50 (4,0 ... 5,0) |
Stabilisator
an Längsträger |
35
... 41 (3,5 ... 4,1) |
Kontermuttern
der Stabilisator-Endstücke |
40
... 50 (4,0 ... 5,0) |
Federbügel |
25
... 36 (2,5 ... 3,6) |
Hinterfeder
vorn an Bodengruppe |
35
... 41 (3,5 ... 4,1) |
Hinterfeder
hinten an Bodengruppe |
11
... 14 (1,1 ... 1,4) |
|